Conventional e-waste metal recovery processes, such as electrorefining and smelting, can result in unpredictable outputs, high energy consumption, and costly long payment settlements. Our innovative process simplifies metal recovery from e-waste using a proprietary two-step process of digestion and electrowinning to produce a high-purity copper cathode for sale and regenerating reagents offering a clean and cost-effective alternative to other e-waste recovery solutions.
How emew compares to alternative
e-waste metal recovery methods
Shipping to a smelter
emew clean technology
- Independent in-house solution with full process control
- 100% precious metals realization from the feed, with fast value access
- Onsite solution with predictable yield of high-grade copper, sold direct for premium price
- Ability to recover tin which is three times as valuable as copper
- Lower carbon emissions due to no transportation and no smelting
Outsourced smelting
- Tough terms negotiations, no control over the process, and multiple stakeholders
- Precious metals uncertainty or loss due to inaccurate sampling and long payment time
- Unpredictable yield with longer settlement times
- Limited ability to recover tin, value lost as well as penalties if tin is found in feed
- Increased carbon emissions from smelting and transport of waste to the facility
emew clean technology
- Fast metal realization within 24 hours
- Lower working capital, flexible operation, and scaling
- Ease of precious metals refining and filtration
- Ability to recover tin which is three times as valuable as copper
- Closed loop system with full metal accountability and simple air permitting
Outsourced smelting
- Processing time approximately three weeks
- High initial outlay, costly, and hard to scale and maintain
- Higher sludge generation with precious metal loss in filtration
- Limited ability to recover tin, and value is lost
- Higher carbon footprint, metals reporting, and stringent air permitting required
Why customers choose emew for
e-waste recycling
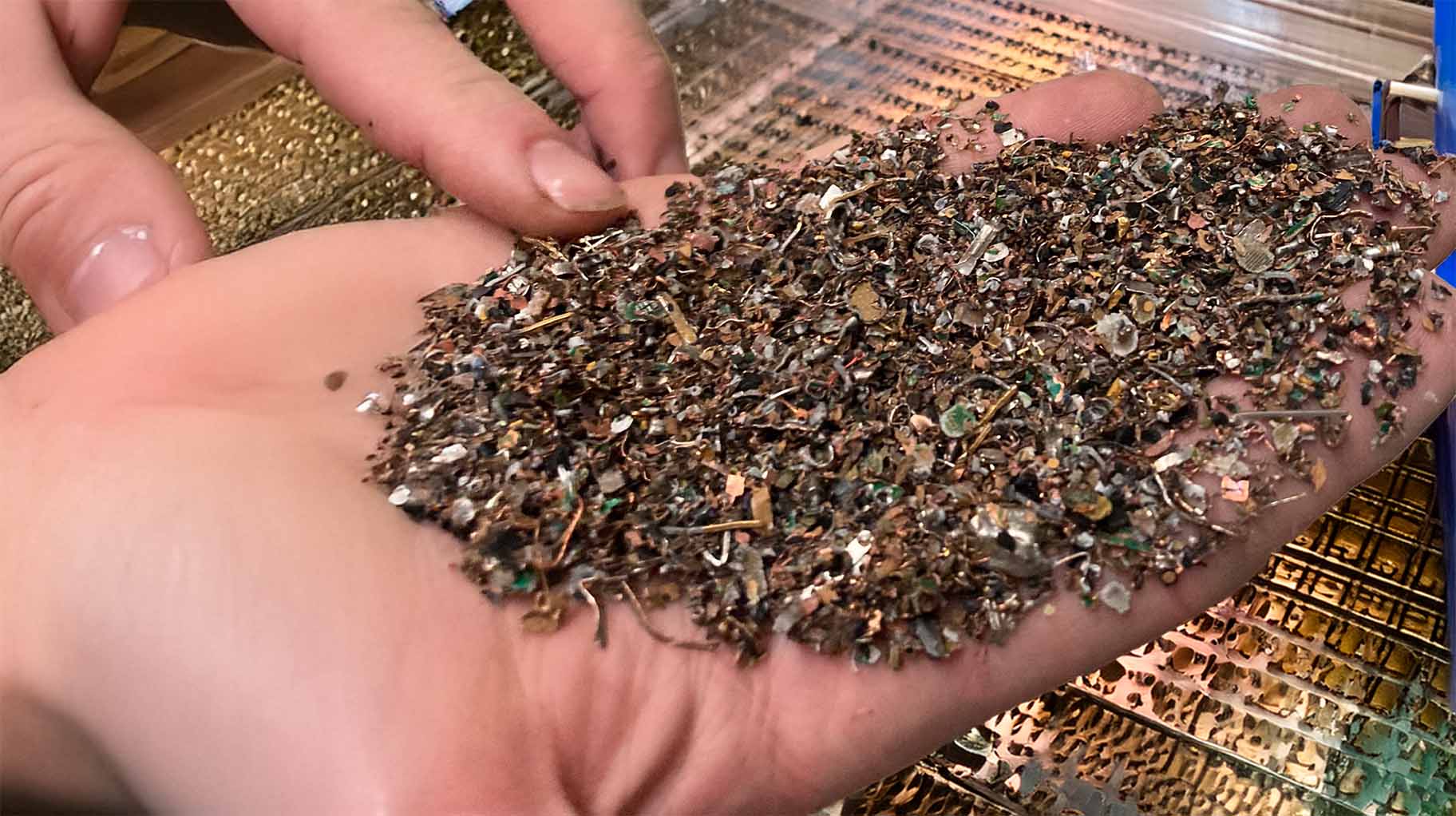
Challenge:
Using an in-house electrorefining method to recover metals from e-waste, our customer faced several drawbacks, including the need to melt fresh anodes, remelt spent anodes, and deal with additional stripping requirements for equipment and labor. This process generated more sludge and loss of precious metals during filtration while requiring a high initial capital investment. Additionally, it took over three weeks to access precious metals, with tin being lost in the process.
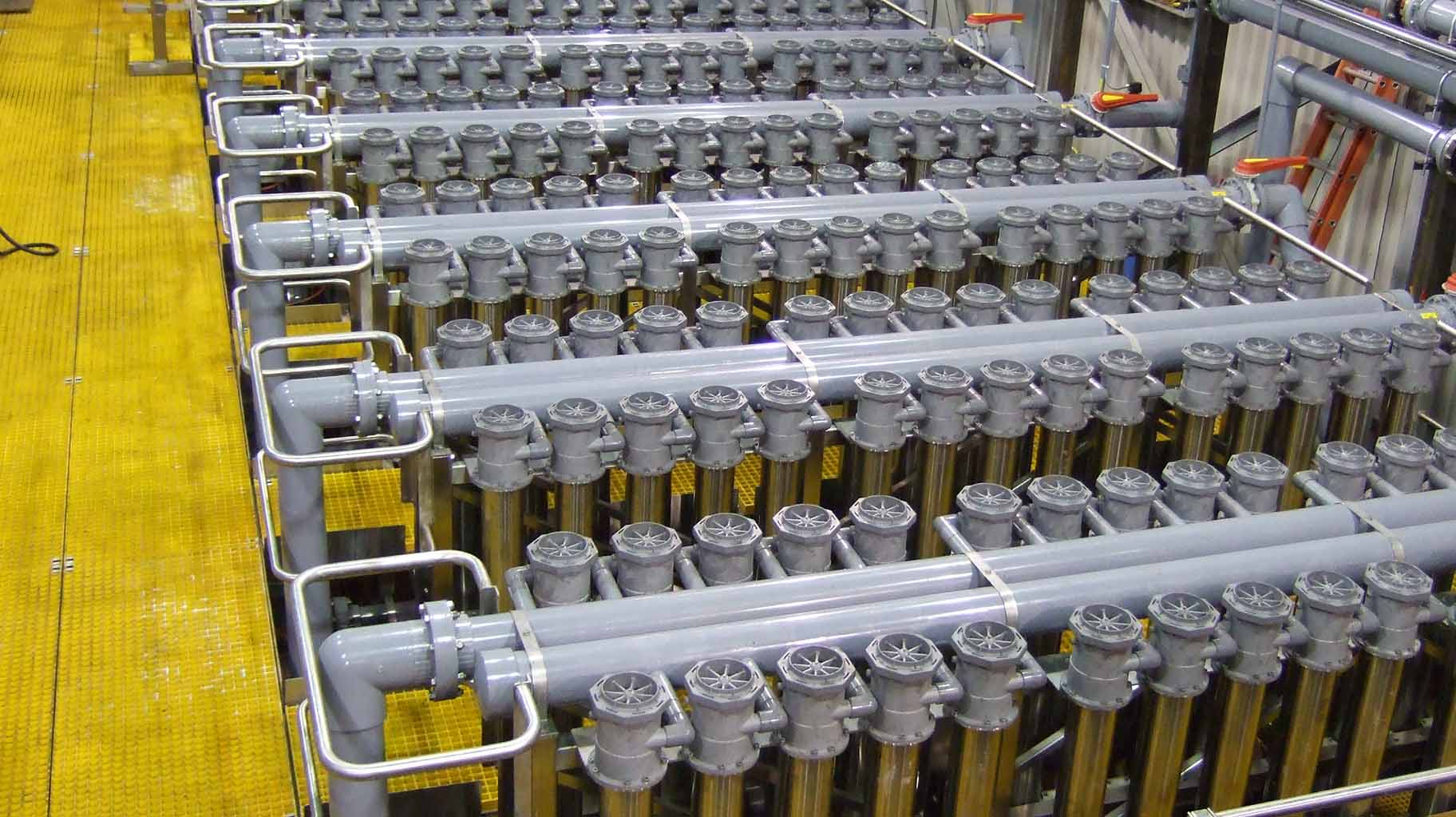
Our customer adopted emew’s clean technology solution for e-waste metal recovery, transitioning from a "shred and send'' model to a local e-waste facility, reducing their environmental impact. Our technology digests base metals and concentrates precious metals within 24 hours for faster precious metal value realization. The process produced high-purity copper cathodes for resale or re-use, creating a fast, closed-loop system with lower operating costs and higher financial returns.
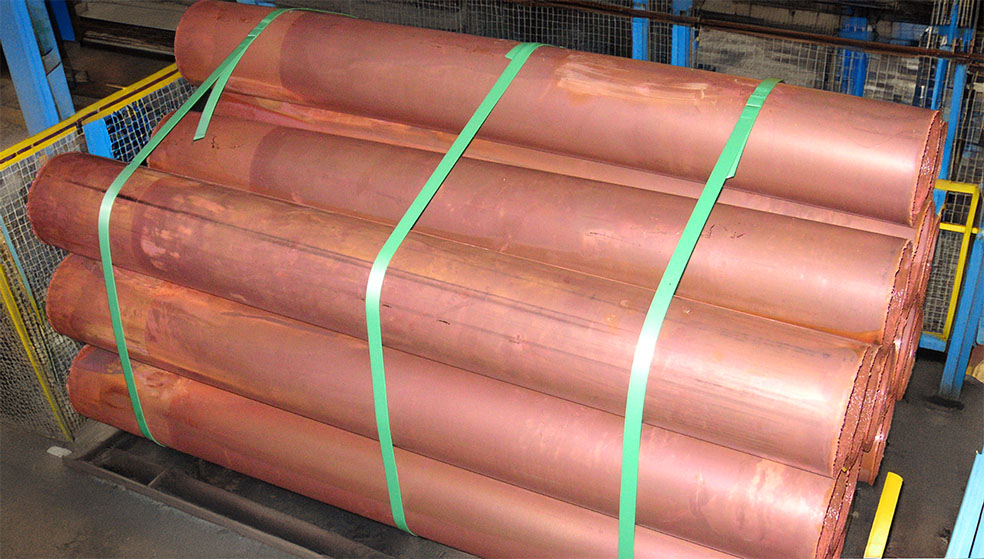
Result:
Implementing emew's flexible on-site solution enabled the customer to recover 100% of precious metals efficiently and securely, as well as numerous other benefits:
- Independent recovery of 100% of precious metals within 24 hours
- Production of premium oxygen-free copper for direct sale
- Recovery of tin previously lost during smelting
- No need for casting or remelting of anodes, easier cathode stripping, and easier filtration
- Modular solution allowing scalability
- Full metals accountability due to the closed-loop system
- No air combustion products and a low volume of gases