By avoiding SX/IX processes or copper sulfide/iron precipitation, emew offers a safer, more efficient method of copper removal from lithium-ion batteries. Our two-step method overcomes challenges related to conventional lithium-ion battery recycling by extracting over 90% of copper selectively from the black mass leachate, transforming it into high-purity copper cathodes for direct use or resale. This on-site solution offers process simplicity, greater financial returns and lower environmental impact.
How emew compares to traditional lithium-ion recycling methods
emew clean technology
- Simple process using one technology system for copper removal and recovery
- Safer system with no acid mist or lead anodes and zero additional reagents and solvents
- Onsite solution enables direct production of foil grade copper and premium resale price
- Lower initial outlay, lower circulating load, no manpower for stripping or ventilation hoods
- Closed loop system with high current efficiency, lower power consumption and smaller footprint
SX/IX + electrowinning
- SX or IX prior to electrowinning requires additional equipment and maintenance
- Ventilation and PPE required for acid mist, safe disposal of lead anodes required, SX reagents pose fire risk
- No foil grade copper production, lower resale value and ROI
- High circulation load, high expenditure for additional manpower and equipment
- Complex system, energy intensive process with larger environmental footprint
emew clean technology
- Simple process using one technology and less operator involvement
- Direct onsite recovery of high purity copper for premium resale price
- Lower operating costs, no manpower for stripping or ventilation hoods, lower circulating load
- Direct production of valuable foil grade copper (10% premium) and recovery of nickel
- Safe and sustainable solution with no acid mist, SX reagents or lead anodes and no waste or shipping carbon emissions
Precipitation by sulfide or iron
- Complex manual process, operator dependent
- Low value byproduct with costly outsourced recovery process
- No foil grade copper production, lower resale value and ROI
- High circulation load, high expenditure for additional manpower and equipment
- Larger carbon footprint, highly toxic hydrogen sulfide gas requires rigorous control and handling, waste iron product
Purification challenges in the lithium-ion battery recycling industry
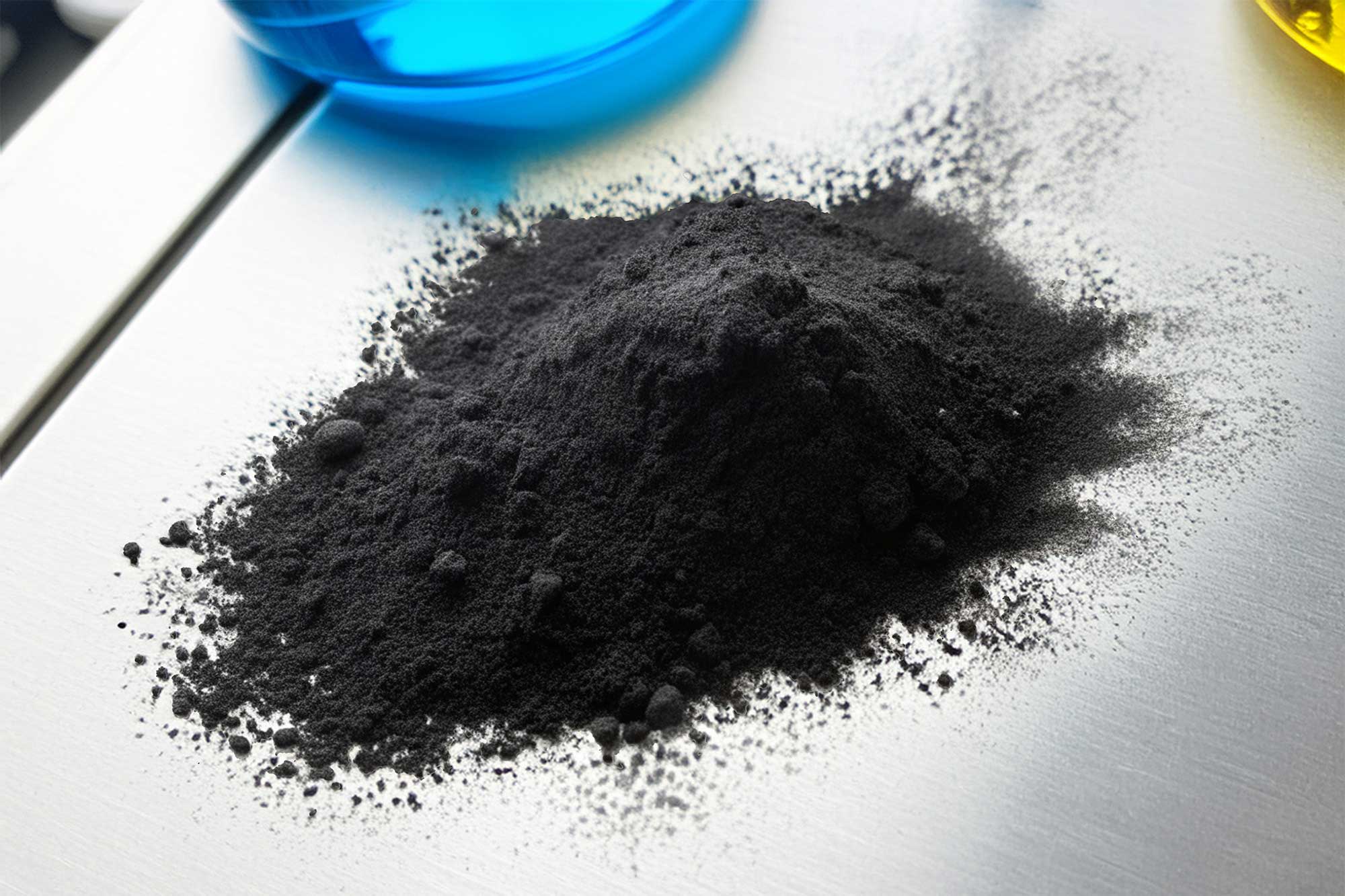
Challenge:
Companies in the battery recycling industry face purification challenges due to processes that often involve SX/IX combined with conventional electrowinning. This method requires significant manpower, equipment and space, leading to high operational costs. It also emits acid mist, requires PPE due to flammable reagents and produces low-value copper byproducts, posing safety risks alongside increased expenditure and carbon emissions.
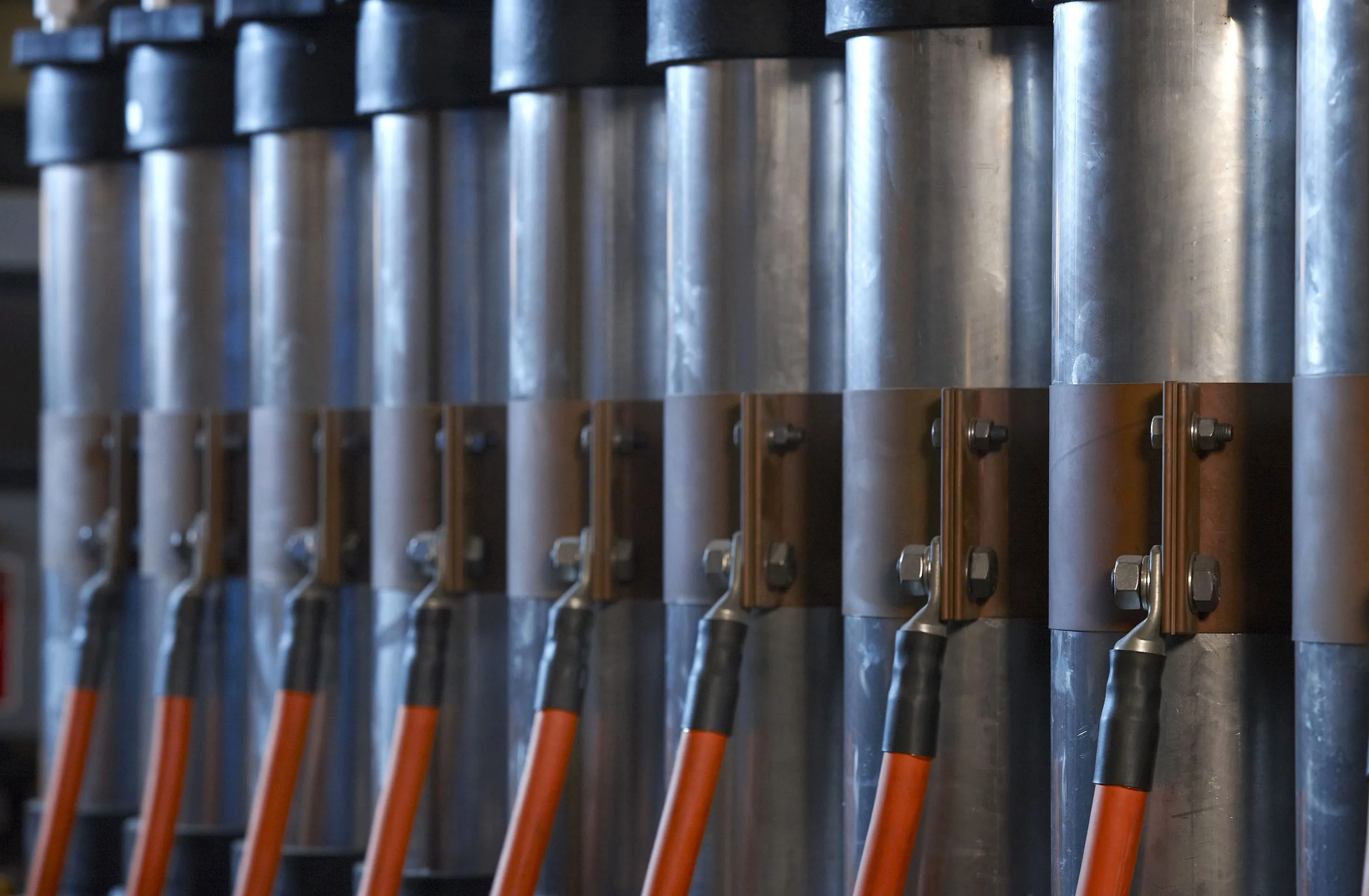
Solution:
Our innovative technology solution eliminates the need for SX/IX or copper sulfide precipitation, offering a two-step method for copper recovery. The emew process is capable of extracting over 99% of copper from the black mass leachate and removes copper entirely from the solution, producing high-purity copper cathodes suitable for foil, alongside battery-grade salts in subsequent steps.
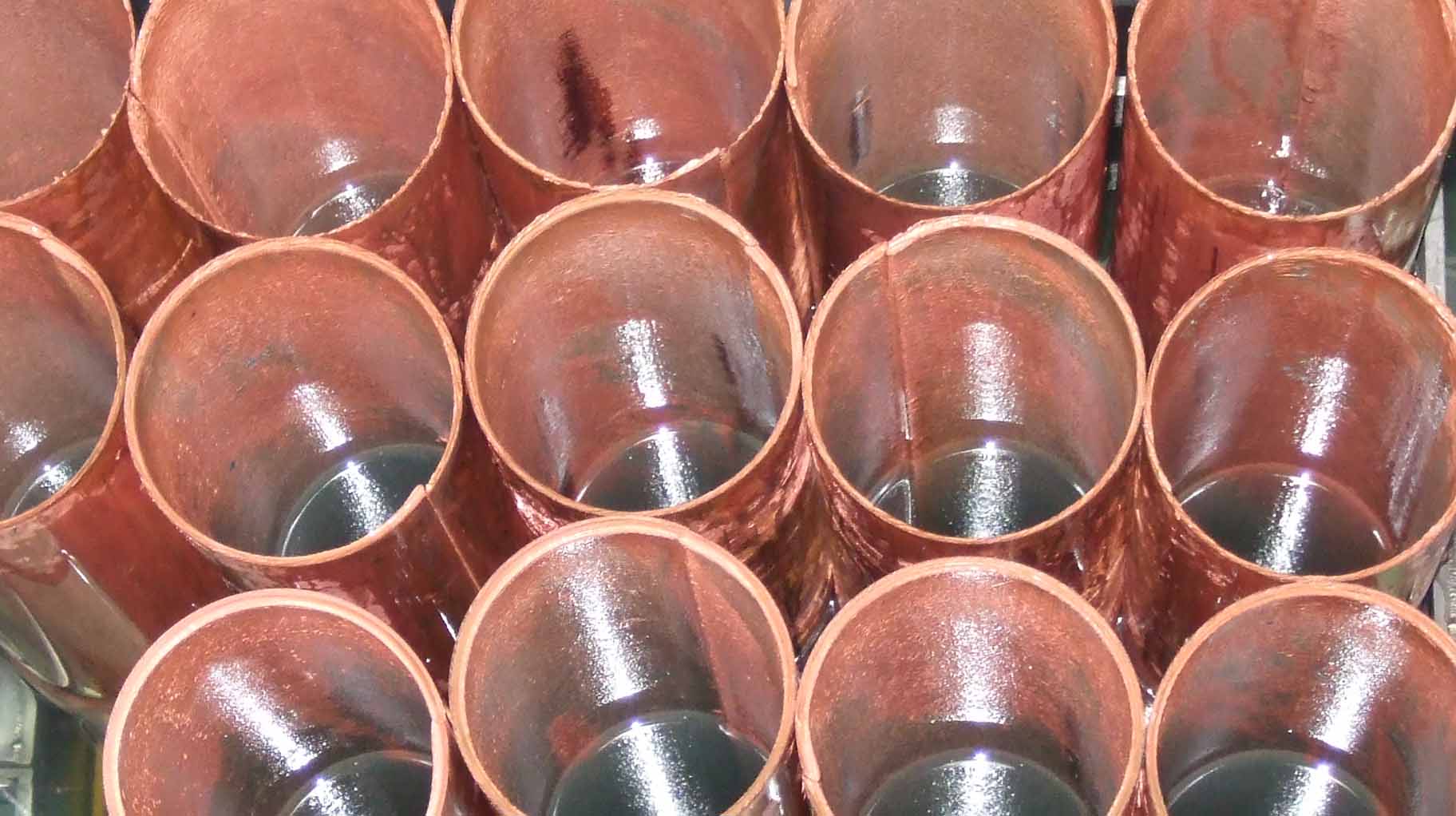
Result:
The emew on-site solution for lithium-ion battery recycling enables our customers to directly recover and resell valuable high-purity copper, alongside numerous other benefits:
- Higher premium for oxygen-free copper
- Lower working capital and OPEX due to reduced manpower and no ventilation hoods
- Zero additional reagents or solvents required
- Increased safety with no acid mist or SX reagents