Recovery of precious metals and base metals from electronic waste
What if I told you that we send hundreds of millions of dollars to landfill every year? If you look around the room you are in right now, you will likely see a multitude of electronic devices. Our reliance on electronic devices in everyday life is growing and rapid technological advances continuously bring updated models onto the market. This means that more devices are being discarded, with more being sent to landfill than ever.
Several base and precious metals make up essential components of electronic devices. The properties of these metals make them ideal for recycling and reuse. Yet, studies have shown that only 15-20% of electronic devices are recycled. This leaves a huge untapped volume of valuable metals that could be sold or reused instead of sitting in landfills. Effectively recovering metals from these devices could have multiple ecological benefits from reducing the economic burden of electronics recycling to reducing the demand for mining ore.
1. The scale of electronic waste
Electronic waste (referred to as E-waste) is the broad term given to waste containing electronic components ranging from computers to commercial machinery. E-waste is categorized as hazardous waste due to the presence of toxic chemicals such as mercury, lead, and brominated flame retardants. E-waste is a complex mix of plastics and metals and coupled with hazardous chemical components make proper waste management both laborious and costly. Due to these issues, a high proportion of E-waste is sent to landfill with very little being recycled.
According to the Global E-waste Monitor 2020, 53.6 million tonnes of e-waste was dumped in landfills in 2019 alone – an equivalent to the weight of 350 cruise ships. This represents an increase of 21% in five years. An estimated $57 billion worth of gold, silver, copper, platinum, and other recoverable metals was dumped and burned rather than recovered and reused.
E-waste poses a large environmental issue; however, it is also a largely untapped unconventional resource of base and precious metals. In 2019 the United States collected and recycled about 15% of the e-waste. Europe has tougher regulations for e-waste recycling and today stands at about 42.5% recycling rate, which is significantly better than the world’s average.
However, there is room for improvement.
E-waste contains several base and precious metals such as gold, silver, copper, nickel, and palladium. Having an effective method to extract these metals means they can be reused or if the metals are extracted at high purity, can be sold to offset the cost of processing and recycling E-waste. These metals are typically found in printed circuit boards, making them the most metal-value components. This makes printed circuit boards an attractive resource for metal recovery, however, they contain a diverse and varied mix of metals, soldering, and polymers. This composition complicates the recycling process and necessitates the development of technologies to improve metal recovery.
2. The value in metal recovery
The majority of metal value lies in the Printed Circuit Boards (PCBs) of the electronic equipment and metal content varies depending on the type of the e-waste. E-waste is classified into 4 categories – Cat1, Cat2, Cat3, Cat4.
Cat1 includes large household appliances like fridges, washing machines, air conditioners, stoves, etc. Cat2 represents smaller appliances like vacuum cleaners, toasters, microwave ovens, and such. Cat3 WEEEs include computers, phones, and other IT and telecommunication devices like phones, personal computers, and tablets. And Cat4 represents mass electronics like TVs, monitors, audio equipment and speakers, video cameras, etc.
These categories help us to classify PCBs according to their grade and calculate value based on the metals content. For example. Cat1 and Cat2 are known to embed low-grade PCBs while Cat3 and Cat4 WEEEs embed high-grade PCBs.
In the table below we can see base and precious metals content in PCBs based on their category classification.
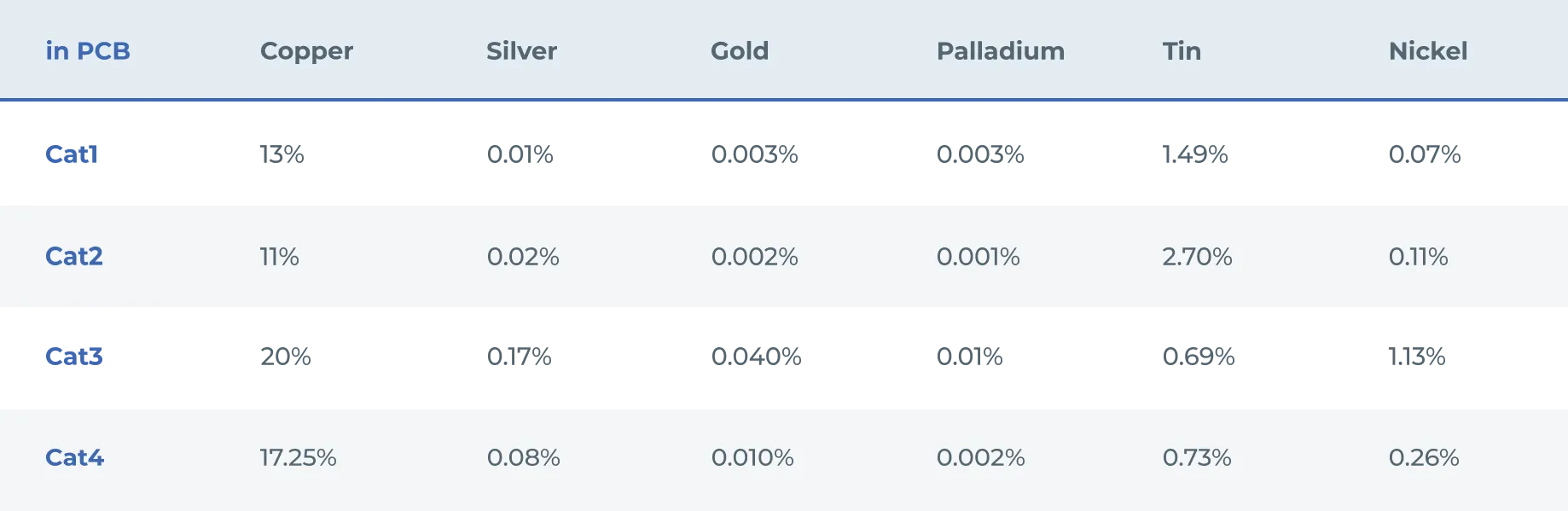
Table 1: Focus metals’ concentration in PCBs of different e-waste categories.
Based on the data reported by Global E-waste Monitor 2020, we have the ewaste generated for each of these 4 categories. With a guesstimate of PCB % in each of the categories, we can have the quantity of waste PCBs in each category and the corresponding market value for each metal (as of 2019):
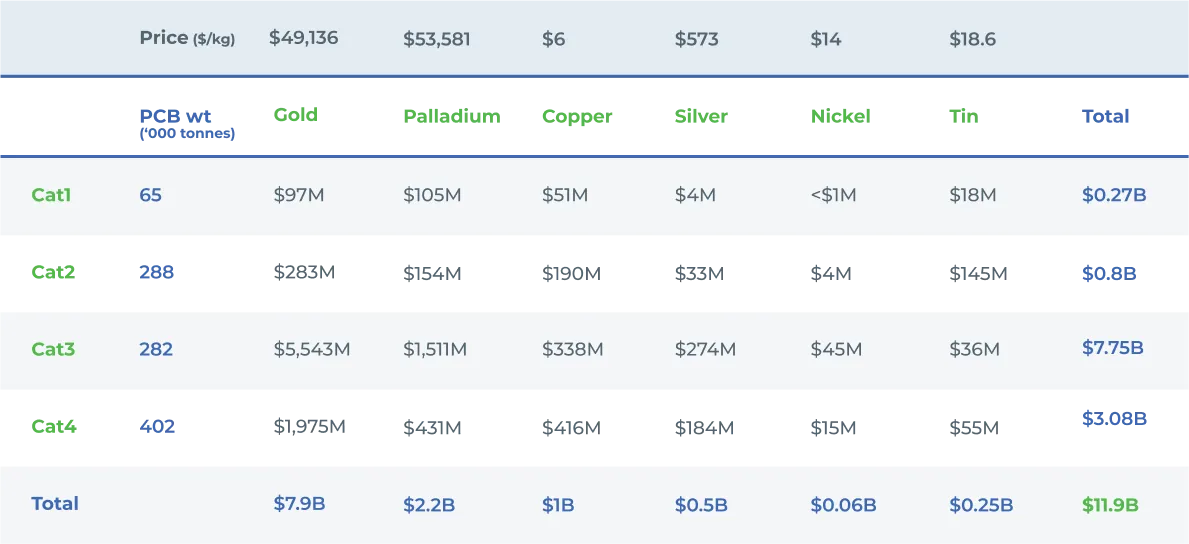
Table 2: The average value of each metal in different e-waste categories in 2019. *Price per kg of metal is the average price for 2019. The total prices and calculations are an estimate. The prices and values are in US dollars.
Based on the projection of an increase in e-waste generation, the world was expected to produce 7% more e-waste in 2021 compared to 2019. Assuming the distribution of e-waste between the categories didn’t change, the quantity of global e-waste and PCBs in different categories are as follows:
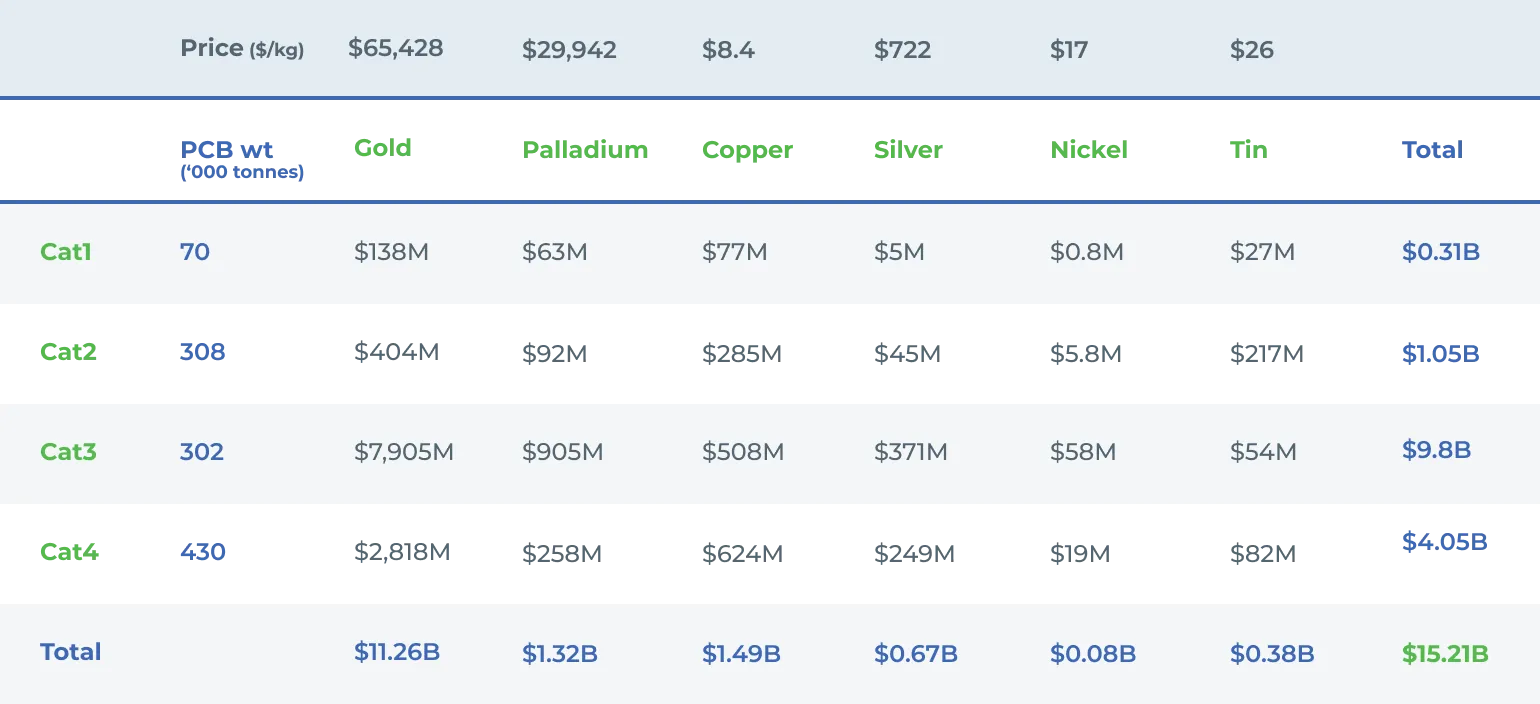
Table 3: The value of each metal in different e-waste categories. *Based on prices of metals of February 2024. The total prices and calculations are estimates. The prices and values are in US dollars. The assumption is made that PCB wt. for different categories of e-waste is the same as in 2021.
As we can see from the table above, the total potential metal recovery from the e-waste market is currently valued at around $15B and the amount of e-waste is projected to grow at a 3.5% year-over-year rate. The highest gold content electronics belong to the Cat 3 of e-waste.
In the following chart we can see a distribution of metals in the e-waste by value, rather than by metal content:
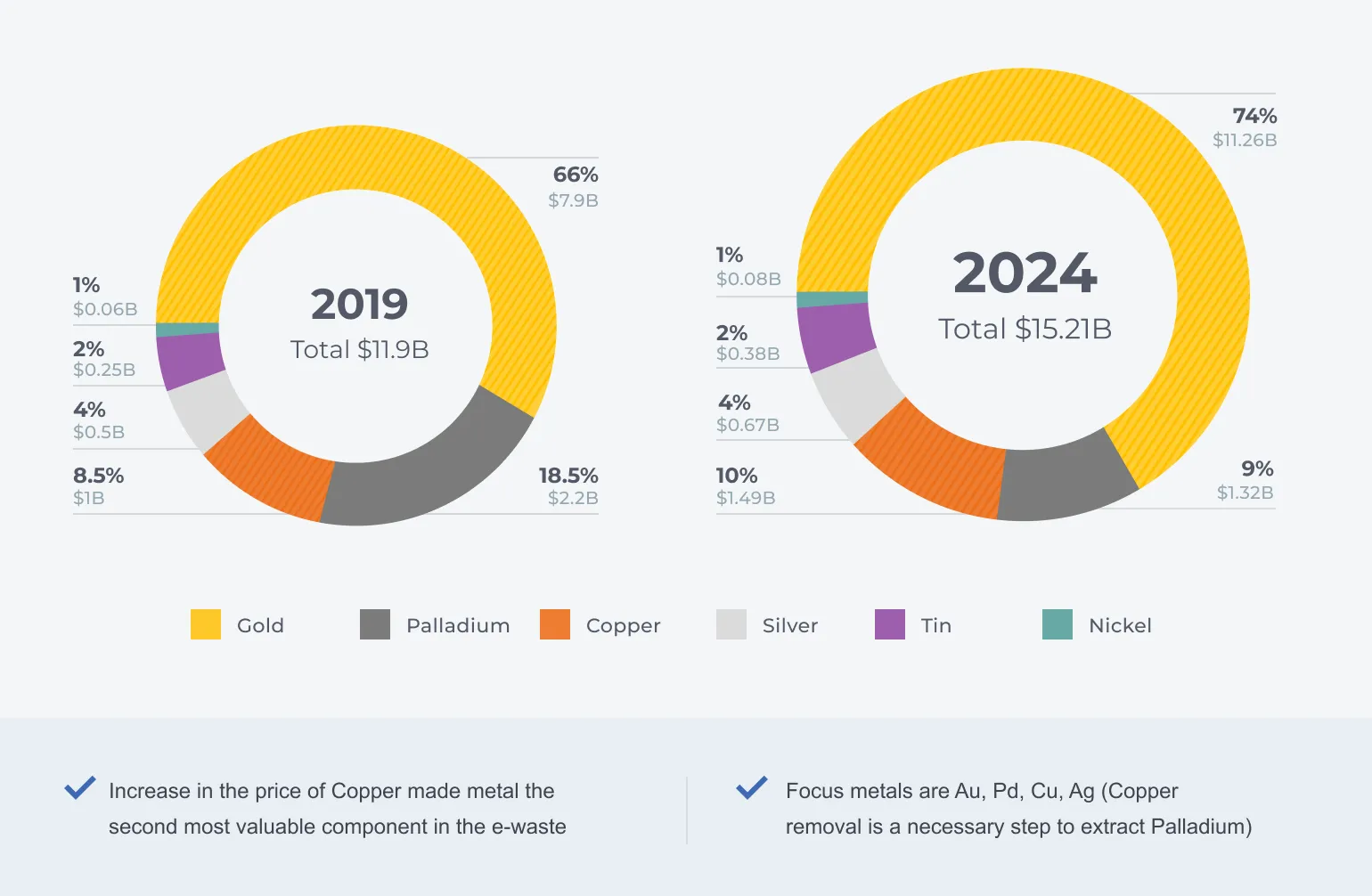
Palladium, Gold, Copper, and Silver combined represent close to 97% of the value of all the non-ferrous focus metals in the PCBs and represent the greatest opportunity for precious metals recovery from electronics.
3. Processing routes for e-waste recycling
Electronic waste can come in a variety of shapes, sizes, and complexity, from smart fridges to handheld game consoles. This means that the extraction and recovery process cannot be uniform for all devices making the sorting and recycling process more complex and requiring several processing steps before the metal extraction process can begin.
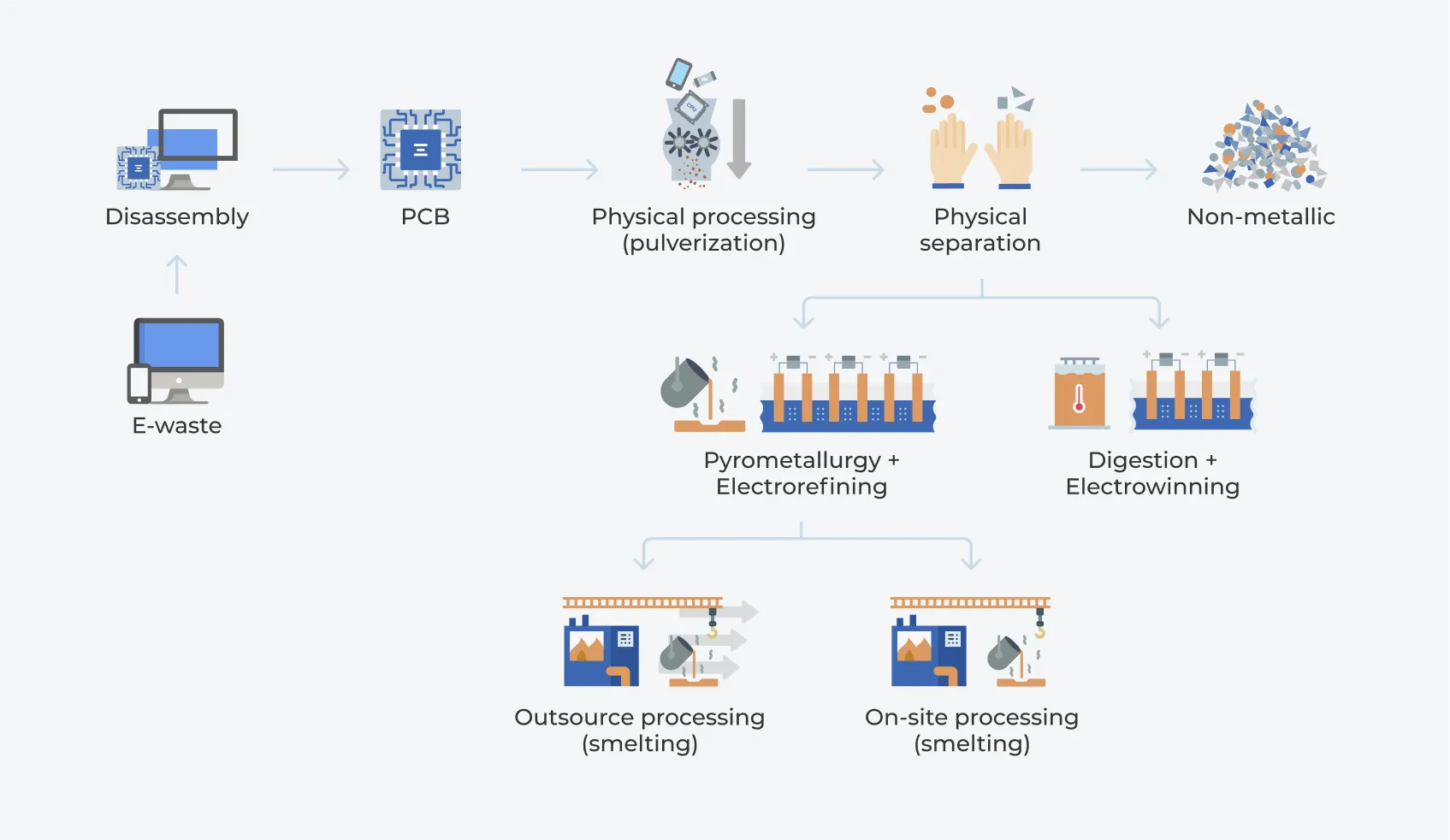
3.1 Physical/Mechanical separation
The first step in the sorting process involves disassembling the electronic device into smaller components and removing hazardous components. These components can then be sorted into materials for recycling and other metal-containing fractions, such as printed circuit boards. The disassembling process typically requires a large amount of intensive manual sorting of materials before moving on to the next step. More autonomous disassembly and sorting methods are starting to be developed. For example, Apple has developed “Liam and Daisy”, robots that are capable of disassembling multiple iPhones at once and recycling components for reuse. The development of autonomous sorting may reduce labor costs and simplify the sorting phase.
The next step is physical processing to reduce the metal-containing components into smaller fractions, including reusable components and printed circuit boards. It includes multiple stages of size reduction using shredders, grinders, or pulverizers to break the components down into manageable pieces.
There are a few key methods utilized during the physical sorting of metal and non-metal fractions.
Shredding or pulverization alters the shape of metals and non-metals. Some metals are malleable and take on a spherical shape under pressure, while non-metals remain nonspherical. This shape effect alongside different specific gravities can be taken advantage of in order to separate different fractions.
Liquid-based sorting uses the different specific gravities of metals and non-metals to sort into fractions. Processed PCBs are placed into a liquid solution, often tetrabromoethane or acetone and non-metals float nearer the surface while metals sink nearer the bottom. Liquid sorting is a straightforward process; however, the efficiency is low and is affected by particle size and shape.
Another process is electrostatic separation. As given away by its name, this process separates materials based on the ability to conduct electricity. Non-metal fractions that do not conduct are sorted out using a vibration screen. The limitation of this method is that it is limited to only small particle sizes.
Finally, magnetic separation is used to recover ferrous metals, such as copper. Magnetic separation is only effective when done prior to crushing. Magnetic separation is performed first and followed by crushing and then undergoes electrostatic processing.
Physical sorting has a number of major limitations that prevent its large-scale use. The sorting methods produce a high potential for losing precious metals and not recovering metals to high purity. Additionally, there are high operating and energy costs to using these methods.
3.2 Metal extraction
After the mechanical separation is completed, we are looking at three different options for further feed processing that are currently used to recover both precious and base metals from PCBs.
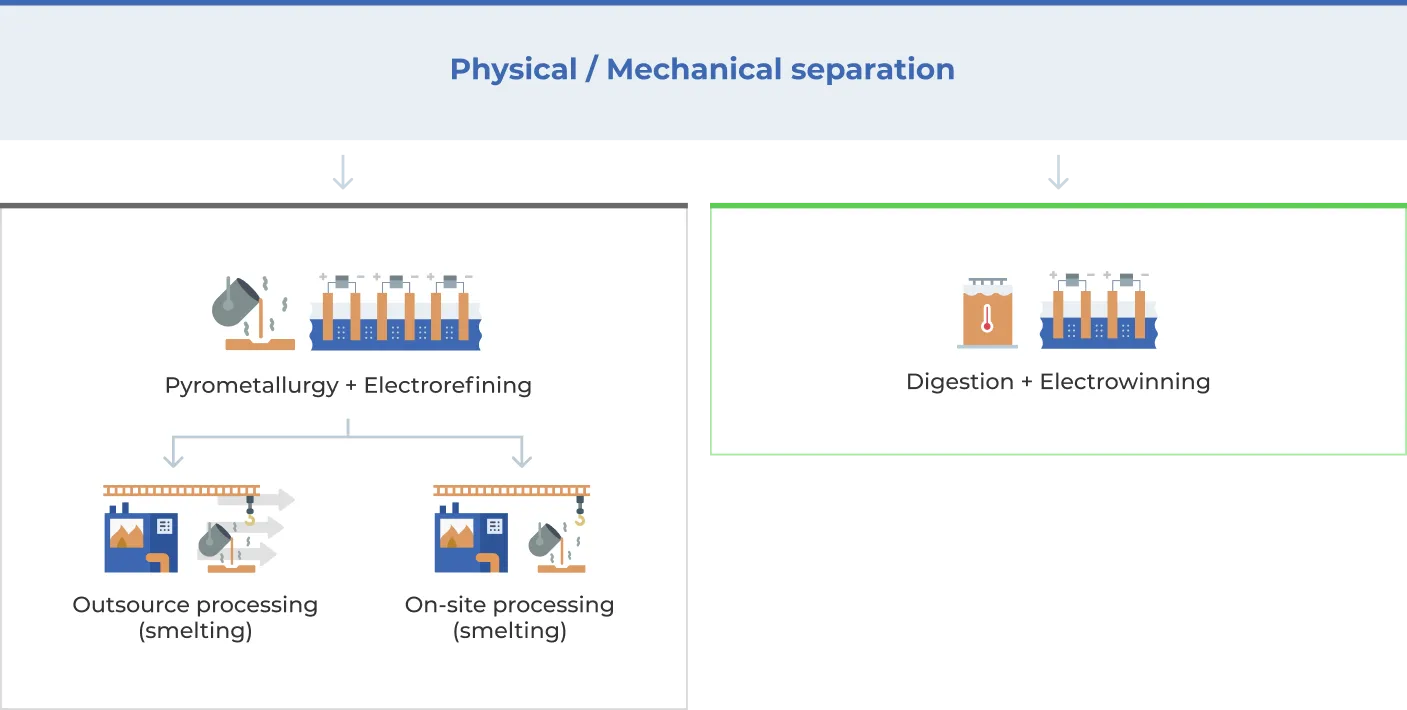
3.2.1 Pyrometallurgy + Electrorefining
Smelting is currently one of the most commonly used processes with up to 70% of PCBs treated in smelters. Essentially, crushed PCBs are incinerated and smelted in furnaces. This method only partially removes the impurities. As a result, a low-concentration PGM alloy is produced which requires the base metals to be removed before the PGMs can be processed. The recovery of base metals from integrated smelters is limited to copper, as iron and aluminum become concentrated in the slag produced. PCBs also contain ceramics and glass which contribute to higher slag formation, leading to a greater loss of recoverable precious and base metals. On top of the high energy consumption, smelting has a high risk of dioxin formation and other hazardous toxins release. There are sophisticated pollution abatement processes to control any discharge into the atmosphere.
An additional step required for further metal processing is electrorefining. In the electrorefining process anodes are cast from smelted, molten alloy and pure copper cathodes are produced in the electro-refining cells. During the electrolysis, copper will dissolve into the solution and plate in its pure form as a copper cathode. Noble metals like gold and PGMs do not dissolve into the solution but fall to the bottom of the cell (or anode bag) generating anode slime every 15-20 days. Other less noble metals dissolve at the anode but do not plate well, resulting in impurities build-up and electrolyte contamination which requires bleeding to maintain copper cathode quality.
Another option is to recover the precious metals within 24 hours by utilizing the digestion and electrowinning process. This will eliminate the requirement of anode casting, as well as the handling and recycling of spent anodes. The same will be discussed in 3.2.2.
Outsource processing (smelting)
Some e-waste recyclers choose to outsource further feed processing to third-party facilities to avoid the capital investment and operational headache of refining. In most cases, these plants refine metals via the smelting (or pyrolysis) route.
While smelting processes are generally very effective at processing large volumes of materials, it is difficult to determine the exact composition of different lots processed in a smelting line and accurate pre-sampling can be difficult if the materials are not homogenous. Shipping costs can be high and working capital can be tied up if the returns from the smelter take several months.
Disadvantages of outsource processing:
- Lower value realized
- High shipping costs
- Prolonged payment terms
- Locked working capital
- High carbon footprint
On-site processing (smelting)
In some cases, recyclers build their own smelting facilities that are very similar to the third-party smelters but normally smaller in size. They face similar environmental and operational challenges but extract the actual value of metals and don’t incur shipping costs.
Disadvantages of on-site processing:
- Smelting permits are hard to obtain and highly capital intensive
- Requires additional processing steps
- Higher working capital in the precious metals
- High carbon footprint
3.2.2 Digestion + Electrowinning
Another route that e-waste recyclers take is digestion combined with other purification technologies. This method uses a combination of caustic or acid leaching followed by a purification technique. There are several different metal purification techniques including cementation, ion exchange, solvent extraction, activated carbon adsorption, and electrowinning.
The digestion stage is preceded by preprocessing of PCBs into non-ferrous particles that may contain various metals including gold, silver, copper, and PGMs. During the digestion, the copper is digested while the gold, silver, and PGMs come out as a residue in less than 24 hours and can be further recycled into pure metal or sold to precious metal refineries. You can read more about how to extract gold and silver from electronics with digestion and electrowinning here.
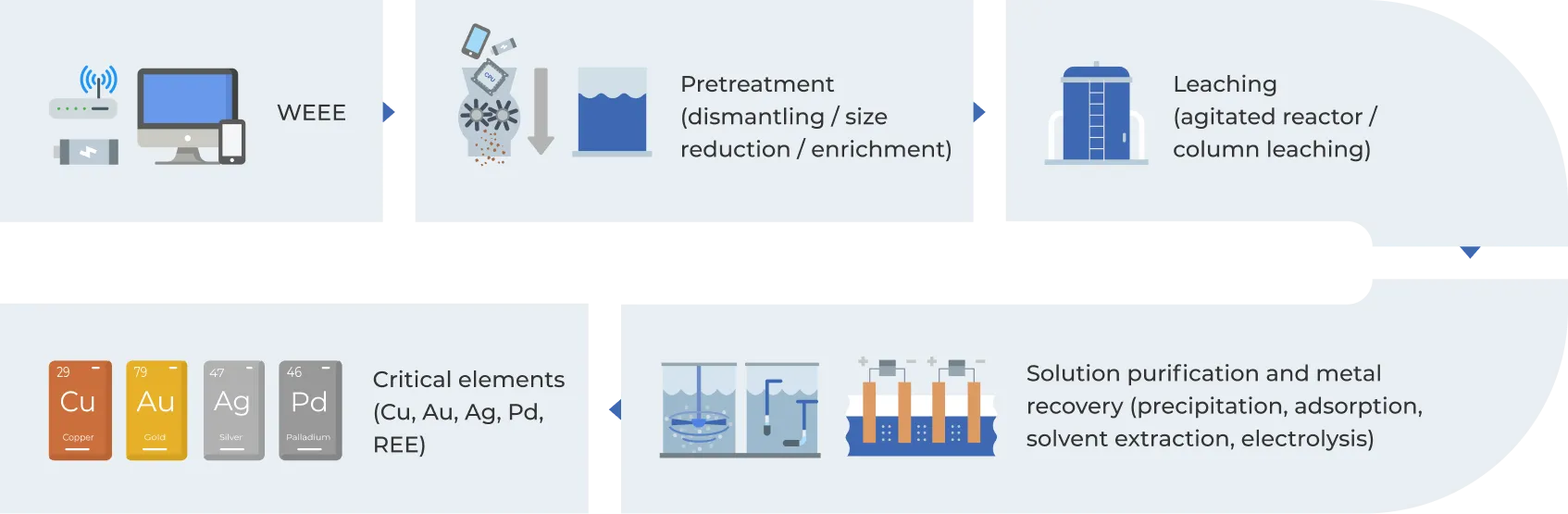
Now that the copper metal is in solution post-digestion, a direct current can be applied, and copper is electro-deposited onto the cathode. The electrowinning method has been successfully recovering copper from the electrolyte in the form of high-purity cathodes. However, there may be other dissolved metals that will compete with copper to electro-deposit on the cathode as an impurity and may require pre-treatment to ensure the production of high-quality copper cathodes.
Conventional electrowinning also has some limitations in terms of selectivity, operating cost, and a safer environment. These conventional cells have low mass transfer rates, offering higher residence time to other dissolved ions near the cathode surface. Once the copper ions near the cathode surface are reduced, these other competing ions also get electrodeposited and reduce the purity of the copper cathode. Another limitation is open cells generate acid mist, making it difficult for operators to work around the cells. As electrowinning is a batch process, conventional cells have difficulty in producing coherent cathodes at lower copper concentrations. The emew electrowinning system overcomes many of these limitations of conventional electrowinning.
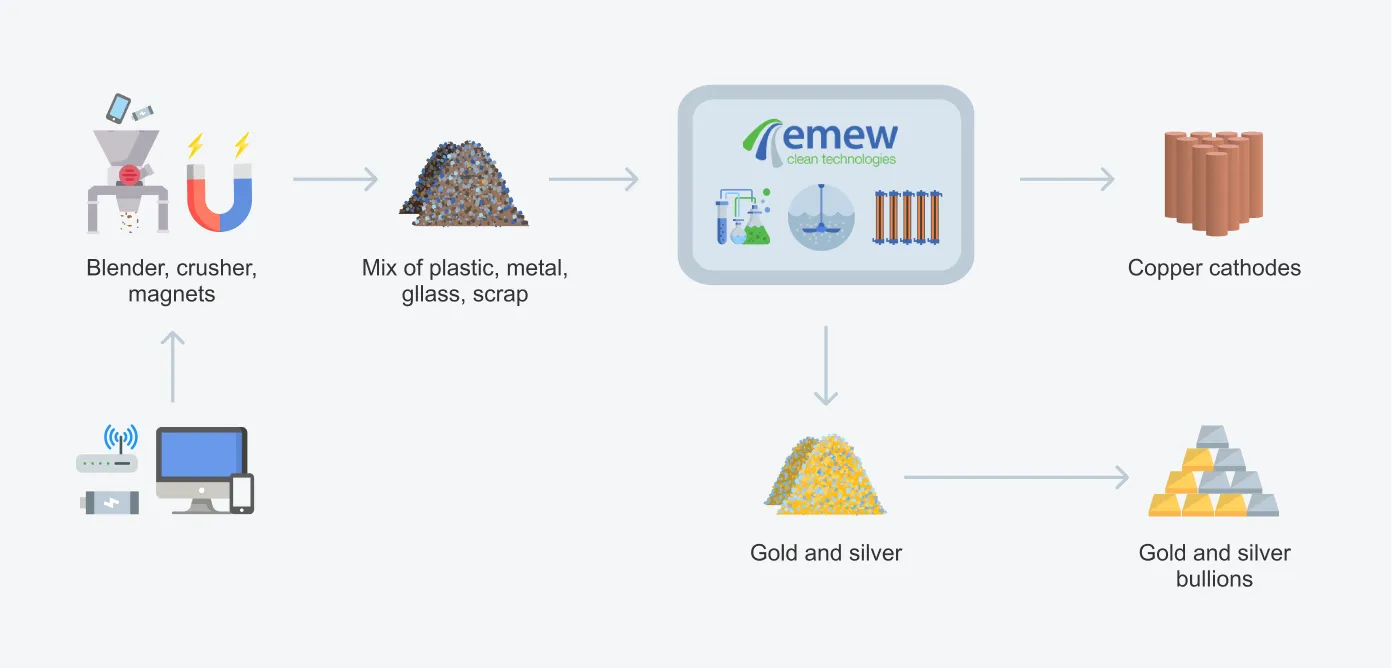
The emew electrowinning system utilizes cylindrical cells where the electrolyte is rapidly circulated across the cathode, improving mass transfer which produces saleable copper cathodes even at lower concentration levels. During the copper electrolysis, acid is regenerated in the cell and can be recycled to the copper removal process thus reducing overall acid consumption and waste generation.
Additionally, emew electrowinning cells are a closed system that overcomes hazardous issues such as acid mist and other noxious gases, making for a much safer working environment. With the emew’s auto-stripping of cathode tubes from starter sheets (mother blanks), there is no requirement for additional stripping equipment that is a necessity in conventional electrowinning cells.
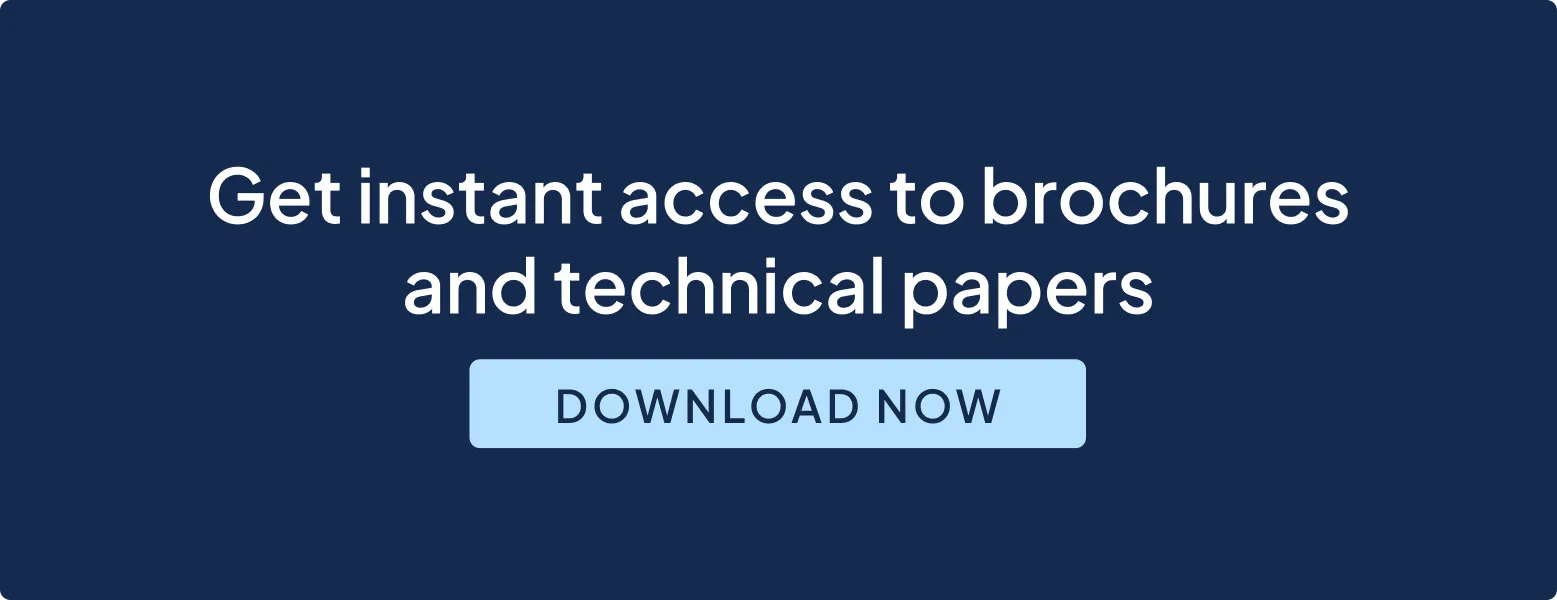
4. Summary
Improper handling of e-waste not only represents a lost financial opportunity but also contributes to global warming. If metals from e-waste are not recycled, we have to invest in mining and refining operations to generate primary metals. Mining is likely to become more expensive due to a decrease in metal grade in ores.
Just to think that the global value of raw materials in the e-waste generated in 2019 was equal to approximately $57 billion USD. And we only managed to recover a small fraction of it.
But changes are coming. Europe and US already recycle close to 40% of electronic waste and other countries are catching up. Since 2014 the number of countries that adopted some form of regulation of e-waste increased from 61 to 78, however, in many cases the enforcement is poor, and recycling is not done properly.
Another option that governments are looking into is forcing manufacturers to recycle their own products or make them pay for the cost of recycling or disposing of them. The idea behind this legislation is that once the producers will have to pay for the cost of recycling, they will invest in making products more easily recyclable. Governments also try to encourage consumers to recycle their old electronics through education and awareness. It was proven that when the collection of e-waste is made convenient and easy for consumers, the municipalities start seeing high collection volumes.
There are many advantages and disadvantages in every processing route.
As metals recovery from PCBs and other types of electronics becomes more financially feasible and more strictly regulated, new sustainable and green technologies are being developed with the goal of making recycling simpler and more efficient. It is our job to make urban mining a reality, preserve the environment, and contribute to the circular economy.
Have a question about your application? We will be happy to chat!
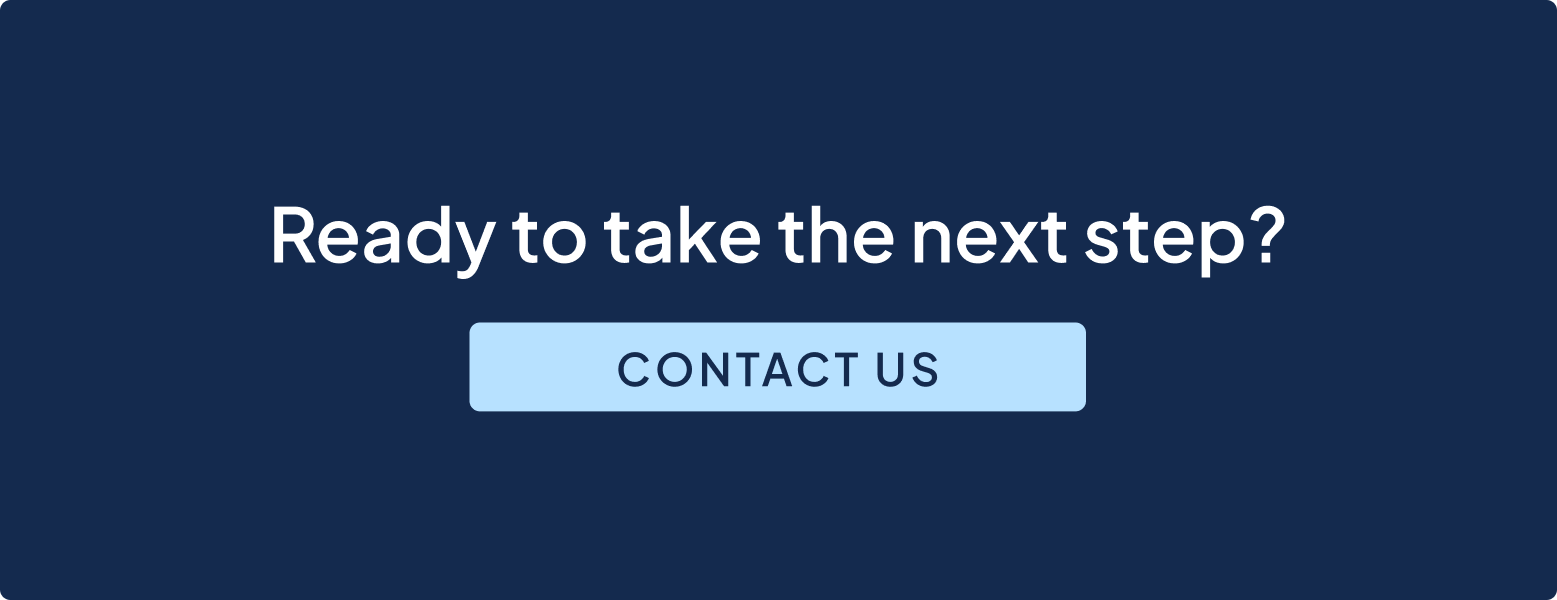
Additional resources
In this video, Dr. Michael Korzenski provides valuable insights into the extraction of precious metals from electronic waste. He also addressed our queries regarding the value of these metals in e-waste and the techniques employed to recover them.
Sources:
Solving the E-waste problem initiative http://www.step-initiative.org/
Hsu et al (2019). Advancements in the Treatment and Processing of Electronic Waste with Sustainability: A Review of Metal Extraction and Recovery Technologies. Green Chemistry
Kaya, M (2016). Recovery of metals and nonmetals from electronic waste by physical and chemical recycling processes. Waste management
Debnath et al (2018). Sustainability of metal recovery from E-waste. Frontiers of environmental science and engineering.
Memon et a (2017). Design for recovery of precious and base metals from e-waste using electrowinning process. International Journal of Advance Research in Engineering, Science & Technology
Materials (2014) Characterization of Printed Circuit Boards for Metal and Energy Recovery after Milling and Mechanical Separation
Cucchiella, F., D’Adamo, I., Lenny Koh, S.C. et al. (1 more author) (2016) A profitability assessment of European recycling processes treating printed circuit boards from waste electrical and electronic equipments. Renewable and Sustainable Energy Reviews
https://www.sciencedirect.com/topics/chemistry/electrorefining
https://www.epa.gov/sites/default/files/2014-05/documents/handout-10-circuitboards.pdf