What pops into your mind when you see the word, "liberation"?
The word liberation comes from the latin word, liberatus, which literally means "to set free" or "to deliver", and can easily apply to myriad of different topics from politics and religion to science and industry.
Particularly in the copper industry, the word liberation applies to the act of freeing copper specifically from refinery bleed electrolyte. The process that starts with mining and carries on through smelting and electrorefining is complex with many process operations. Let's take a closer look at the story of 'liberating copper'.
On average, mined ore contains about 1% copper and in order to recover this copper from the rock it requires several physical and chemical processing and refining steps in order to produce market ready copper metal.
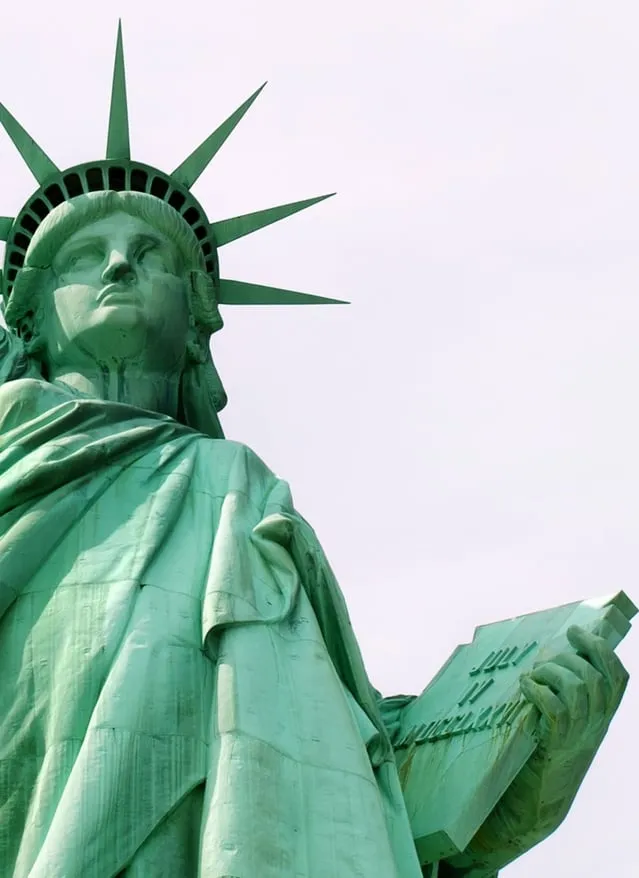
Mining: The First Chapter
The whole process starts with mined ore delivered by the truckload to a mining process facility, often near to the ore pit, where the ore is crushed and milled thereby separating the copper from the waste rock (ie. gangue). The milled ore is then mixed with water creating a slurry before undergoing froth flotation, a process that involves adding various chemical reagents while bubbling air into the slurry causing the copper to attach to the bubbles and float to the surface. Once enough copper floats to the top, it is skimmed off and further concentrated in a thickener and pressed through a filter producing roughly 25%-40% copper concentrate with an 8 - 12% moisture content. The rest of the concentrate is made up of other metals such as iron, nickel, arsenic, bismuth, antimony, etc.. as well as sulfur.
Refining of Copper
Copper refining is a process that involves multiple steps. Usually, it starts with a copper concentrate that is smelted to produce impure copper anodes. Then the anodes are electro-refined to produce an LME Grade A copper cathode (+99.99%).
One of the most important factors in the refining of copper is the control of copper concentration and impurities in the solution. Copper at the anode dissolves into the electrolyte faster than the plating occurs at the cathode. As a result, copper tends to build up in the electrolyte and needs to be controlled.
One way to control the copper and impurities in the refinery electrolyte is through an electrowinning circuit. This process is commonly referred to as a "copper liberation".
Refining: Pyro- vs Hydrometallurgy
Hydrometallurgy is the process where the copper is leached with sulphuric acid and undergoes solvent-extraction to separate the impurities from the copper producing a copper-rich electrolyte and raffinate solution. Using electrowinning, the copper-rich electrolyte is subjected to an electrical current that reduces the copper in the solution to the metal plate at the cathode. This process is typically used for copper oxides when the grade of copper is low.
Pyrometallurgy, as the name suggests, involves high temperatures to refine the sulphide copper concentrate. The concentrate is heated in a furnace in a process called smelting, causing the copper concentrate to separate into two layers, the slag layer which contains the impurities and the matter layer which contains copper reaching varying around 55% purity. The sulfides are driven off and collected as SO2 gas that is used to produce sulfuric acid. The copper matte is mixed with reagents in a converter to rid of the remaining sulfides and oxides to produce blister copper containing 97-98% copper. The blister copper is cast into anodes for electrolytic refining where the impure copper is electro-refined into the pure copper cathode. The process involves passing an electrical current across the copper anode and an inert cathode submersed in an acidic sulphate solution. The impure copper at the anode dissolves into the acidic solution and is deposited at the cathode as pure copper. The pure copper cathode is sold to copper mills that produce finished products such as copper wire, rod, etc.
Liberating the Electrorefinery
Unfortunately, the copper refining process doesn't end there and it is here where this story gets interesting. As we already mentioned earlier, the impure copper from the anodes dissolves into solution and is replated or deposited onto the cathode as pure copper, the dissolution process is faster than the plating process causing a gradual build-up of copper ions in the refinery electrolyte. The copper concentration continues to increase along with other impurities such as nickel, zinc, arsenic, bismuth, antimony, and many others. In order to control the copper concentration and other impurities in the electrolyte, a solution bleed is required, also known as a "copper liberator" circuit. Copper liberator circuits use electrowinning to remove the copper in various depletion stages.
See also: Electrowinning 101: What is electrowinning?
Conventional electrowinning circuits are susceptible to impurities in the electrolyte such as arsenic, bismuth, antimony, etc and therefore as the copper is depleted from solution, the quality of copper cathode produced is compromised. A typical copper liberator circuit using conventional electrowinning produces 'anode' grade copper that is recycled back into the anode casting furnace, while contaminated copper sludge is recycled back to the smelter. This results in a high circulating copper load in the integrated copper complex (smelter-refinery) and high working capital. Furthermore, copper refinery electrolyte contains high arsenic and antimony which under the right conditions can produce arsine and stibine gases, both of which are extremely toxic, when the copper is depleted to low enough concentrations.
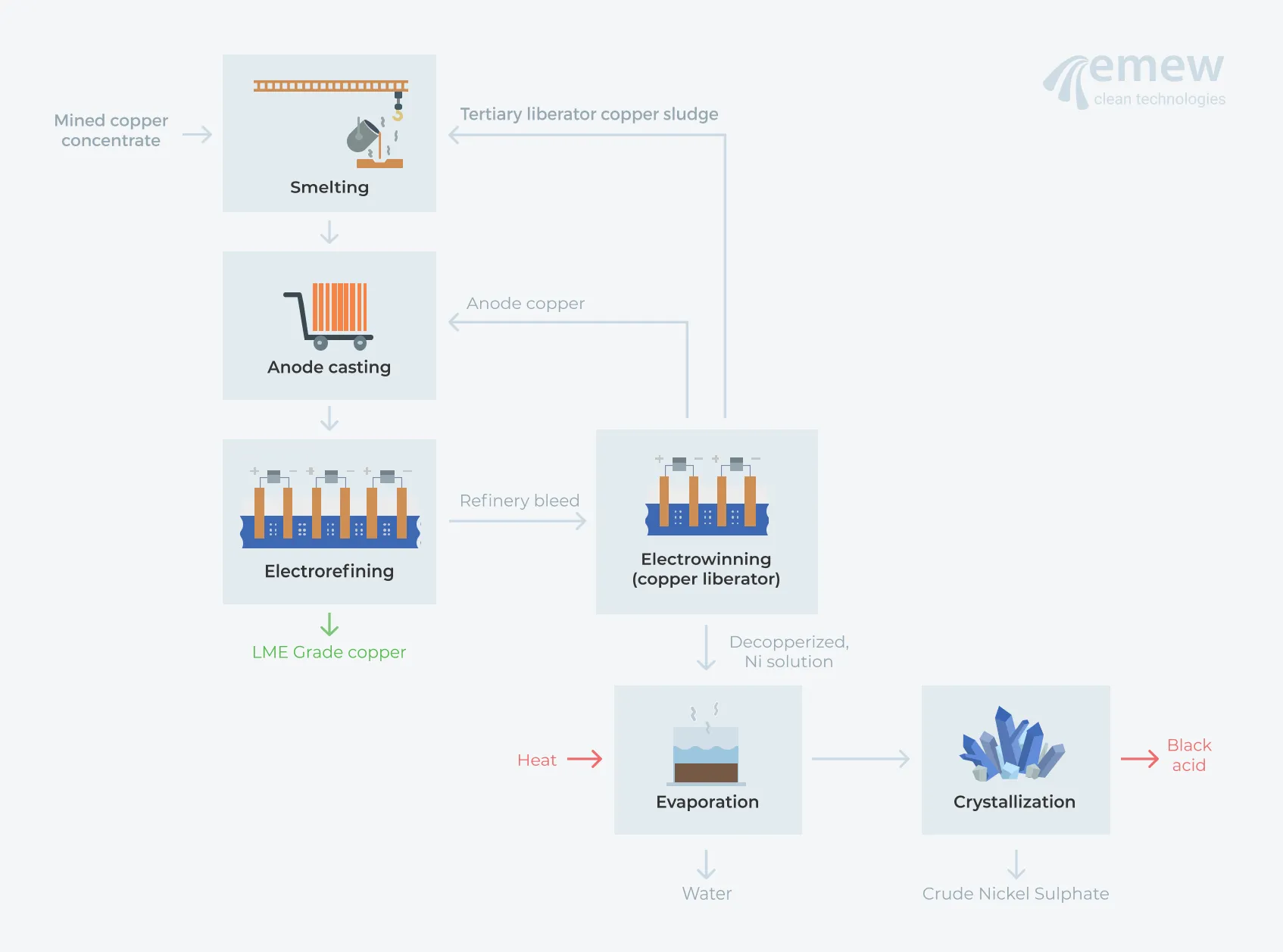
An ideal alternative for copper liberator circuits to recover saleable copper cathode from refinery bleed while improving the health and safety of the liberator operation, is to employ emew electrowinning. The emew cell increases the efficiency of copper plating by using a unique cylindrical cell that significantly increases the recovery efficiency and product purity.
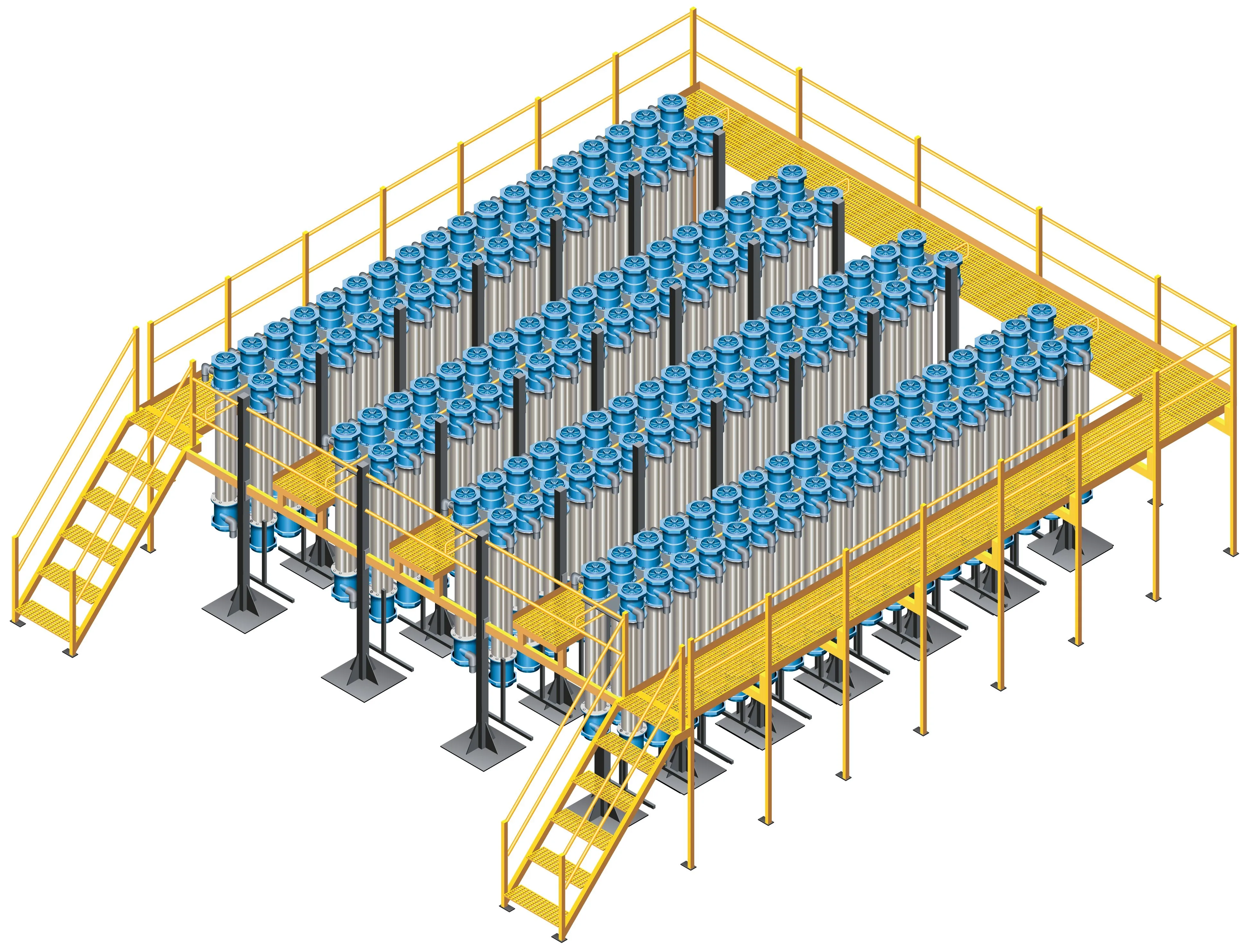
A typical emew liberator circuit produces high purity saleable copper cathode as the primary product, with only a small amount of copper that must be recycled back to the anode furnace. This significantly reduces the recirculating copper load and working capital as well as improving first pass recoveries which decrease operating costs. The closed nature of the emew cell eliminates hazardous acid mist and coupled with the ability to monitor individual cell voltages significantly improves the health and safety of liberator circuits by eliminating the risk of arsine exposure. The now decopperized bleed solution can be further treated to recover the acid and nickel values.
One common method is evaporation to concentrate the nickel with subsequent crystallization to produce crude nickel sulfate (NiSO4) which can be sold 'as is' with the so-called 'black acid' (averaging 20-25% Ni in a sulphuric acid solution) neutralized in a separate treatment facility. Sometimes if the level of nickel is not high enough, additional nickel sulphate is added to aid with crystallization.
Despite the seeming simplicity of this process, many disadvantages are inherent, such as:
- Safety risks - From handling the very acidic black acid, and increased exposure to solutions of high temperatures due to the nature of the evaporator.
- High operating costs - The evaporator requires power to heat the solution, and subsequent treatment or neutralization.
- Unsustainable - The black acid that is produced has low or no market value and is typically sent for neutralization as waste.
So is there a better way to treat the decopperized solution to create more value?
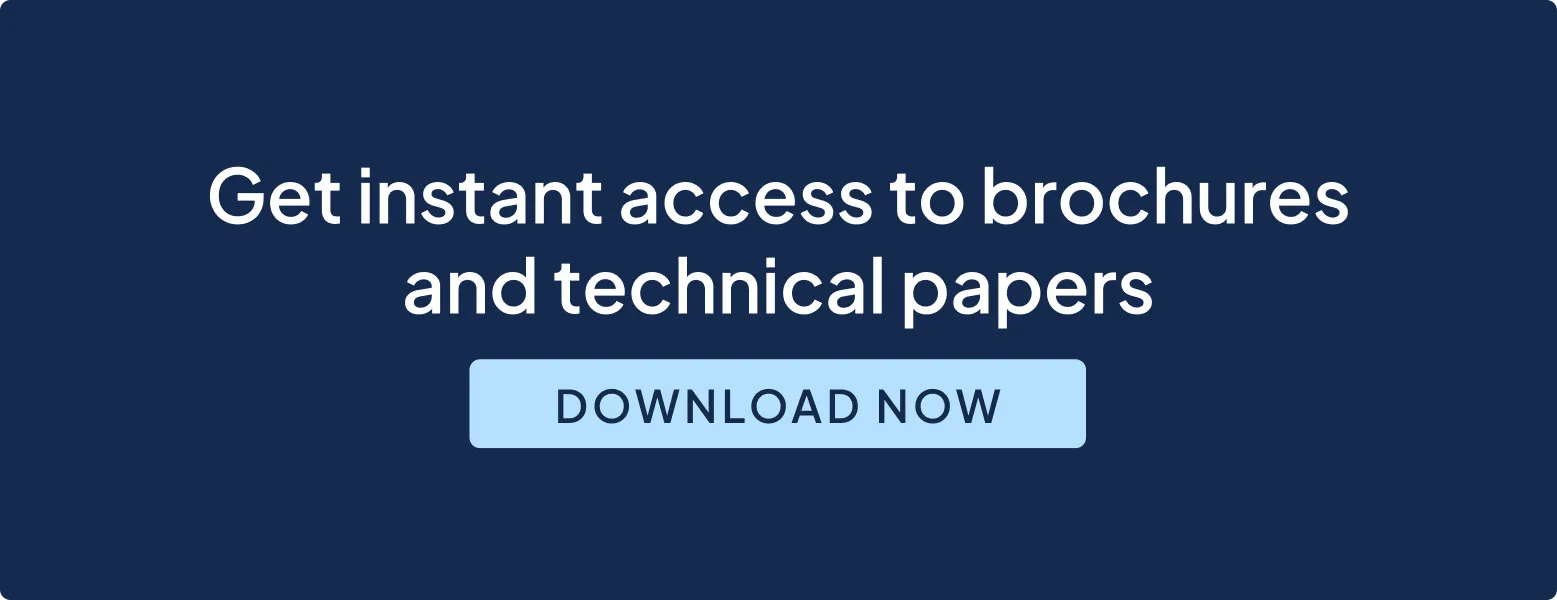
An Advanced Alternative: The Turning point
Many copper refineries that are embracing 'zero discharge' are abandoning evaporation and crystallization, electing instead for an Acid Purification Unit (APU) to treat the decopperized nickel solution using ion exchange to recover the sulfuric acid and produce a de-acidified nickel solution. Now that the sulfuric acid has been isolated from the bleed electrolyte, the concentrated and purified acid can be recycled to the refinery.
The nickel solution is then treated with reagents to precipitate the impurities producing a nickel sulfate solution from which nickel can be electrowon, using, for example, the emew electrowinning cell. The final result is high purity nickel cathode that is perfectly suited for sale. Click here to learn how Hindustan Copper Limited recently implemented a green alternative for copper liberator, acid and nickel recovery by utilizing emew and an APU circuit.
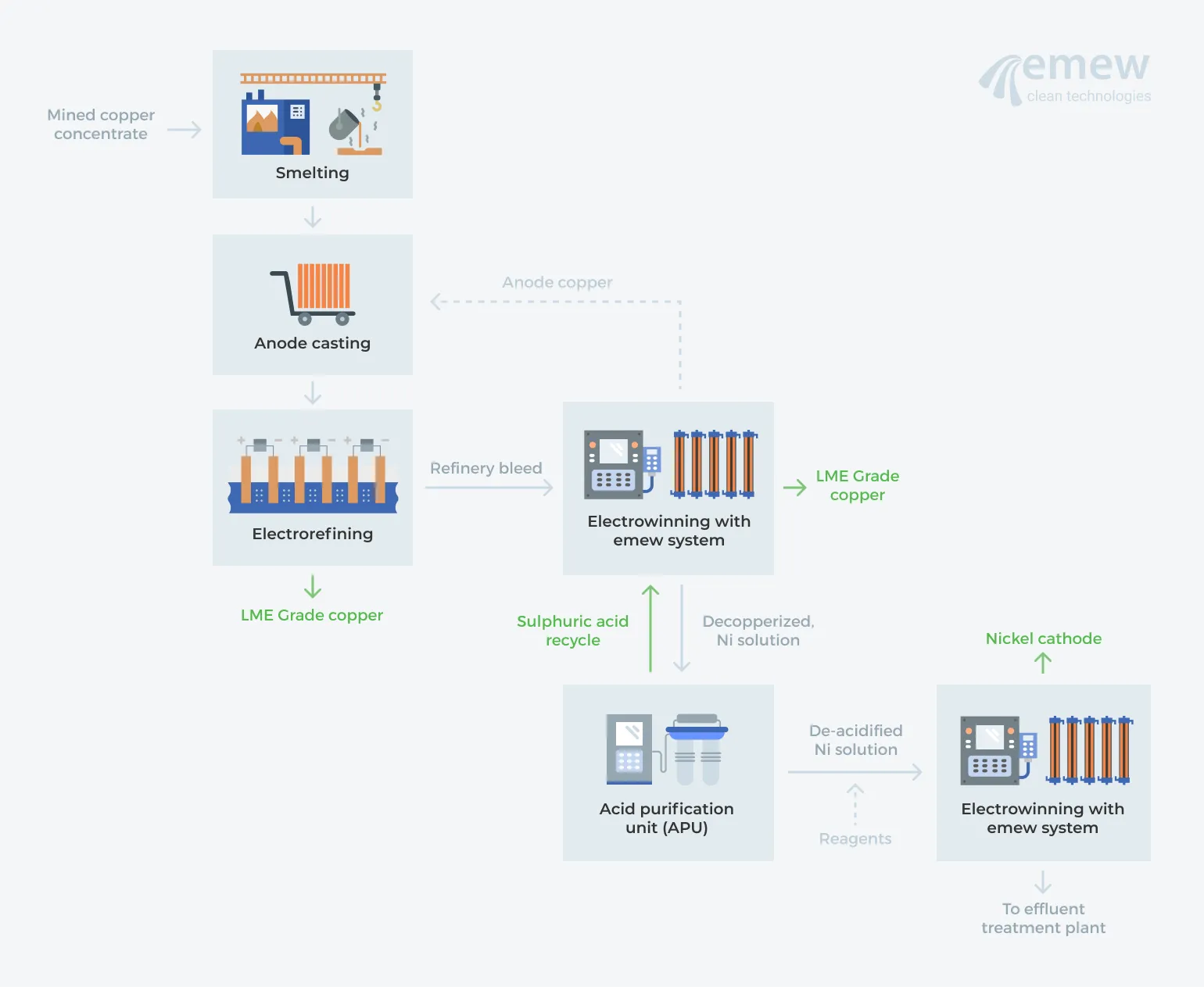
So what's the value for a copper refinery to upgrade their liberator circuit?
Comparing conventional methods of decopperization and nickel recovery with advanced circuits incorporating emew-APU-emew, it is clear that there are many advantages. In summary, an emew-APU-emew circuit will:
- Improve health and safety - There is no tertiary liberator sludge to clean out, no acid mist exposure and no potential for arsine or stibine gas to be generated.
- Lower operating costs - Lower working capital due to fewer copper recycles (less off-spec to anode furnace/smelter), recovery of acid rather than neutralization, significantly lower ventilation requirements, low maintenance and low labour.
- Realize nickel by-product credits - Recover nickel directly as high purity cathode.
- Improve impurity control - Bleed impurities to emew, recover copper and nickel directly as saleable products, high quality cathode from high impurity solutions.
- Enable expansion capacity - More saleable copper from emew liberators coupled with ability to convert existing liberator cells to refining cells to increase refinery capacity.
Are you ready to learn how emew advanced liberators coupled with an APU and nickel recovery can benefit your copper electrorefinery?
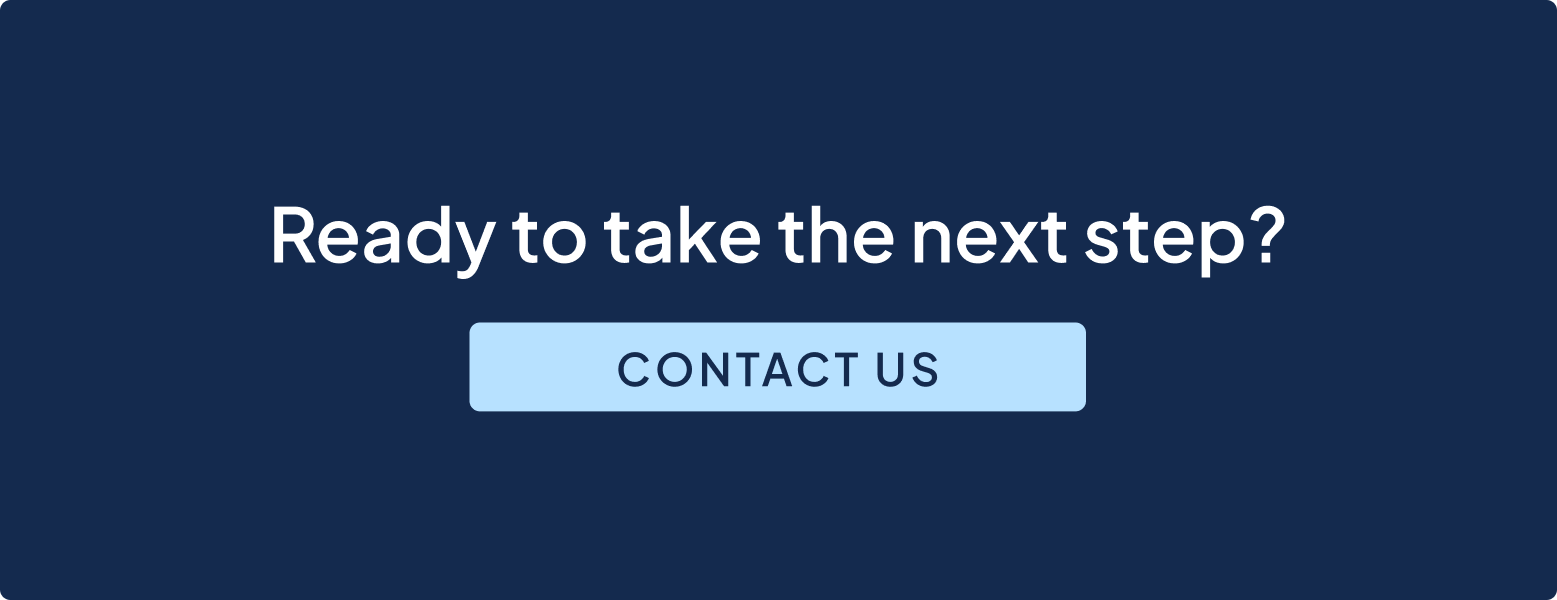
References:
- Copper Smelters - http://www.boliden.com/Global/Smelters/coppersmelters_large.jpg
- Copper Refining: From Ore to Market (2011) - https://investingnews.com/daily/resource-investing/base-metals-investing/copper-investing/copper-refining-from-ore-to-market/
- "Recovery of Nickel from Bleeding Electrolyte Plant at Atlanic Copper," by G. Rios, R. Ramirez, I. Ruiz and I. Gonzalez (2013).