En los EE.UU., durante la escuela primaria, cuando se pensaba en el níquel, la primera imagen que les venía a la cabeza era probablemente esa bonita moneda brillante de 5¢. A pesar de que ya casi no se llevan carteras con monedas, el níquel sigue presente en la vida cotidiana de todo el mundo. Desde el acabado brillante del acero inoxidable en el edificio en donde usted vive, hasta los cuchillos en su cocina, el níquel se encuentra en todas partes. Con el níquel siendo preferido para su uso en el transporte, generación de energía, teléfonos celulares, preparación de alimentos y equipos médicos, se pone uno a pensar de dónde viene todo este níquel.
La verdad es que las reservas de níquel de alta calidad se están agotando rápidamente, y las compañías mineras están buscando nuevas formas de recuperar el níquel, este es un metal base muy codiciado. Me gustaría profundizar un poco más en la recuperación de níquel, específicamente de los minerales de baja ley en la Tierra y, a partir de las soluciones de purga de la electrorrefinación de otros metales.
La importancia de la recuperación del níquel
El níquel es el quinto elemento más abundante sobre la Tierra, con un volumen promedio de 2.7%. Sin embargo, el contenido promedio de níquel de la corteza se estima en un 0.008 por ciento. Con un contenido tan bajo, resulta obvio por qué la minería del níquel es una industria tan importante, y por qué la recuperación del níquel y el reciclaje del níquel se vuelven cada vez más importantes en nuestra sociedad centrada en el consumidor.
El níquel tiene muchas propiedades importantes que contribuyen a su uso generalizado en la industria, estas propiedades incluyen: resistencia a la corrosión, propiedades conductoras y magnéticas, y su capacidad de blindaje electromagnético. Las pastas conductoras de níquel se usan a menudo en los condensadores: estas capas delgadas de pasta se producen mediante polvos con partículas esféricas muy pequeñas, para dar capas compactas que ayudan a aumentar la conductividad. Las partículas gráficas recubiertas de níquel se usan para blindaje electromagnético en sellos, juntas y productos electrónicos de consumo como computadoras portátiles y teléfonos. El desglose del consumo de níquel primario se muestra en la Figura 1, los usos finales del níquel se muestran en la Figura 2.
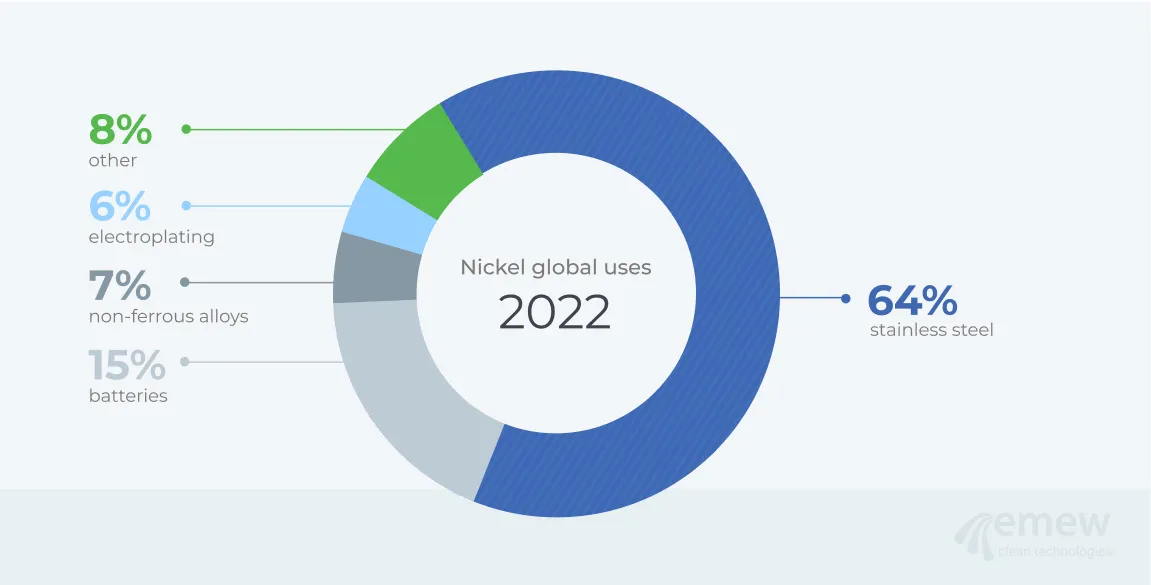
Fig. 1: Consumo primario de níquel
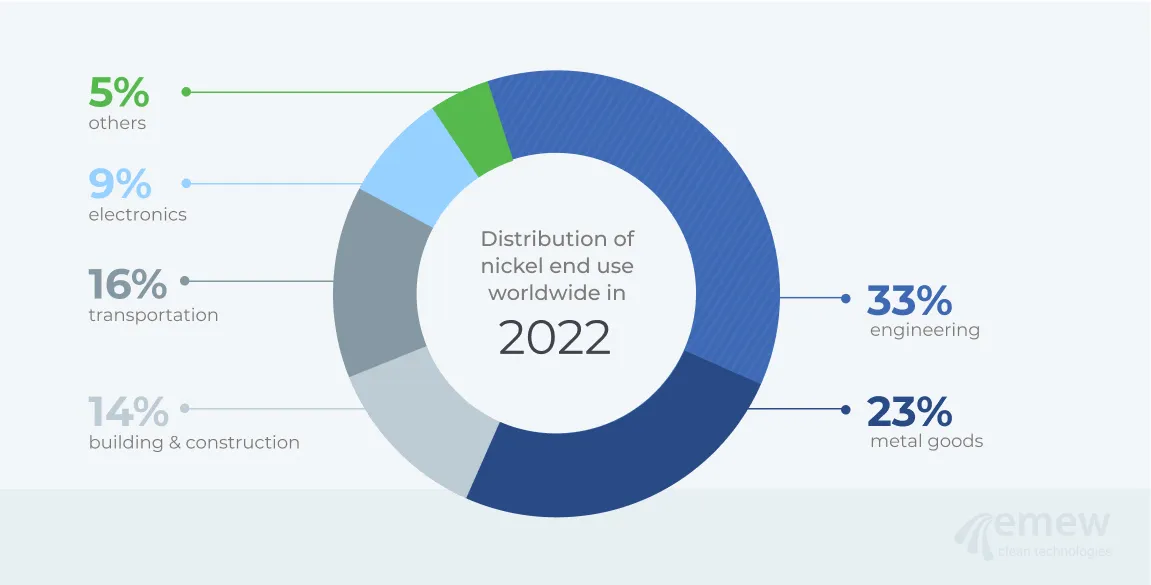
Fig. 2: Consumo final de níquel
En todo el mundo, se usan aproximadamente dos millones de toneladas de níquel cada año: 2/3 de fuentes primarias, y 1/3 del reciclaje de níquel de la chatarra de uso final. En los EE.UU., se informó que se recuperaron 99 000 toneladas de níquel de la chatarra en 2011, en comparación a las 63 500 toneladas de níquel recuperado de la chatarra en 2009, lo que indica que el reciclaje va en ascenso.
Producción de níquel de minerales lateríticos y sulfurosos
En 2009, los principales productores mundiales de níquel eran Rusia, Indonesia, Canadá, Australia y Nueva Caledonia. El níquel se produce principalmente a partir de depósitos de laterita y sulfuro magmático. Las lateritas comprenden aproximadamente el 70% de los depósitos de níquel del mundo, mientras que solo contribuyen al 40% de la producción mundial. La laterita se forma en rocas en climas tropicales y subtropicales, durante largos períodos de erosión, y las lateritas que contienen níquel tienen un contenido promedio de 1 a 1.6% de Ni.
En la actualidad, los depósitos de sulfuro de níquel son la principal fuente del níquel extraído. Las leyes del mineral sulfurado van del 0.15 al 8% de Ni, con un 93% de depósitos conocidos que van del 0.2 al 2% de Ni.
Todos los minerales de níquel tienen un contenido relativamente bajo de níquel, la clasificación es la siguiente: el mineral de níquel de alta ley tiene un contenido de Ni superior al 1.8%, el mineral de níquel de ley intermedia tiene un contenido de Ni del 1.3 al 1.7%, el mineral de níquel de baja ley tiene un contenido de Ni del 0.6 al 1.2%. El níquel se extrae de forma permanente, incluso con estos bajos porcentajes del mineral, porque tiene una gran demanda.
La variación en la concentración de níquel depende del tipo de depósito rocoso que se exponga a la intemperie, p.ej., peridotita, dunita, piroxenita o serpentinita. La laterita se forma a partir de la exposición a la intemperie de la serpentinita, por ejemplo, contiene 45 a 55% de hierro y aproximadamente 1% de níquel, esto se conoce como laterita de hierro niquelífera. El otro tipo de laterita niquelífera se conoce como silicato de níquel, que contiene menos de un 30% de hierro, 30% de dióxido de silicio y aproximadamente 1.6% de níquel. En general, la laterita tiene altas concentraciones de hierro, titanio y óxidos de aluminio.
Con estos bajos porcentajes, no toda la recuperación de níquel de la explotación de laterita es viable económicamente. En 2004, Dalvi, Bacon y Osborne indicaron las siguientes leyes de corte para proyectos de laterita: los proyectos de fundición exigen de minerales por arriba del 1.7% de Ni, y los proyectos de lixiviación exigen minerales superiores al 1.3% de Ni, para que sean viables económicamente. También declararon que los minerales de sulfuro de níquel extraídos por el níquel necesitan una ley por arriba del 3% de Ni para la minería subterránea y por arriba del 1% de Ni para la minería a cielo abierto, para que puedan ser rentables.
Recuperación del níquel y técnicas de explotación del níquel de depósitos lateríticos
Primero me gustaría enfocarme en las técnicas de procesamiento de la minería de níquel de depósitos lateríticos, lo que puede ser un desafío para ejecutarse de manera eficiente. Los minerales lateríticos se tratan con frecuencia mediante procesos pirometalúrgicos, usando un horno para fundir el mineral seco y carbón como agente reductor. Se puede agregar azufre si se necesita de una mata, y se puede seguir refinando para producir ferro-níquel o mata.
Los minerales lateríticos limoníticos (óxidos) generalmente se tratan con métodos hidrometalúrgicos: el proceso Caron y la lixiviación con ácido a presión (PAL), Figura 3. Los minerales con altos niveles de magnesio se tratan mediante el proceso Caron: mediante una reducción selectiva del mineral y lixiviación de amoníaco. Este método consume más energía y produce una menor recuperación de metales.
El método PAL implica el precalentamiento del mineral suspendido y la lixiviación con ácido sulfúrico concentrado a altas temperaturas y presiones. El níquel y el cobalto se convierten en sales de sulfato solubles, y se recuperan de la suspensión en un circuito de decantación a contracorriente (CCD). El CCD implica lavar el residuo y recuperar el níquel y el cobalto solubles. El ácido restante se neutraliza usando una suspensión de piedra caliza, que produce un precipitado de yeso. Se inyecta sulfuro de hidrógeno para precipitar níquel y otros sulfuros. A partir de esto, hay una lixiviación posterior para eliminar el hierro y el cobre, y finalmente la precipitación de níquel mediante la adición de amoníaco, sulfato de amonio e hidrógeno.
Un excelente ejemplo del uso de PAL en minerales de níquel laterítico de baja ley es la mina Ambatovy en Madagascar, una alianza entre Sherritt, Sumitomo y Korea Resources. Esta es una de las minas de níquel laterítico más grandes del mundo y tiene la capacidad de producir 60 000 toneladas de níquel refinado al año, durante al menos 29 años. Esta mina también puede producir 5 600 toneladas de cobalto refinado y 210 000 toneladas de sulfato de amonio.
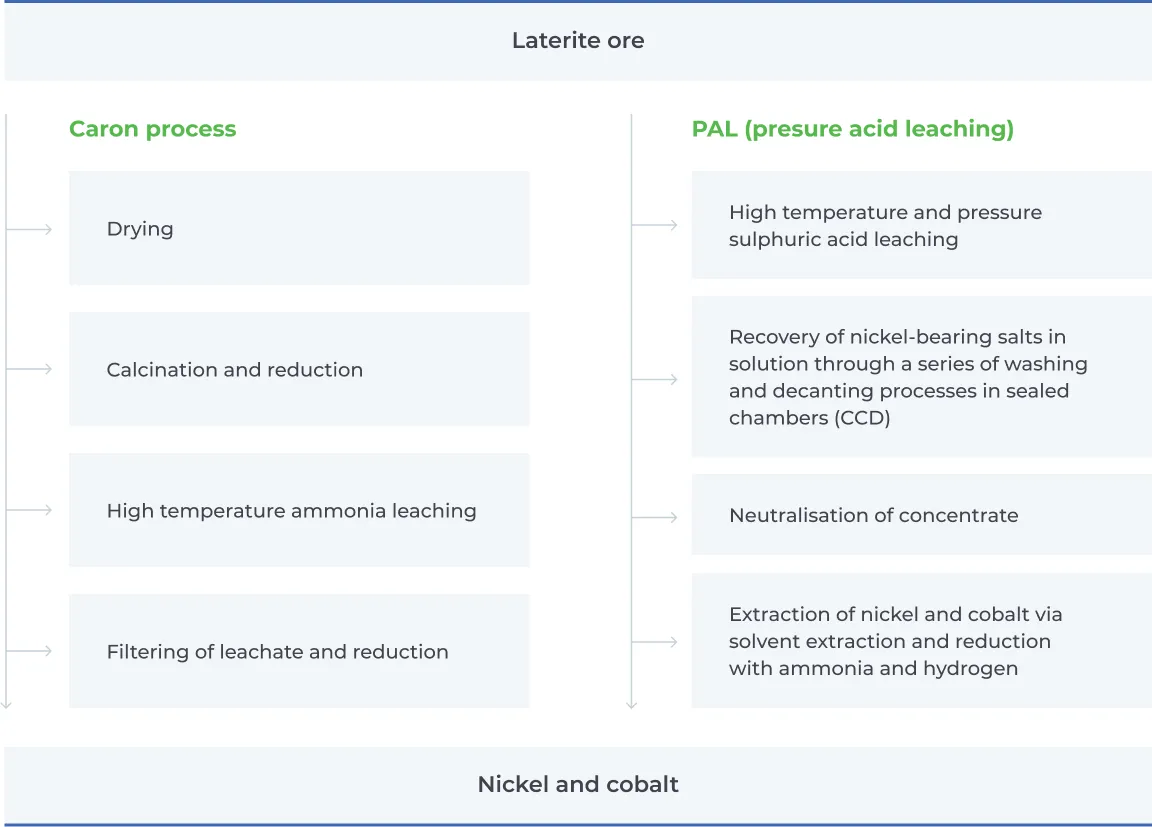
Fig. 3: Hoja de flujo del procesamiento de minerales lateríticos (Natural Environment Research Council, 2008)
Recuperación de níquel y procesamiento de minerales de sulfuro magmático
El procesamiento de minerales de sulfuro magmático es diferente al de los lateritos: los minerales de sulfuro se trituran en varias etapas para separar la mena de la ganga. En cada etapa, el mineral se separa por tamaño, mediante tamices vibratorios, así como la separación magnética de la pirrotina rica en hierro. Después de la trituración, el mineral se mezcla con agua para crear una lechada y se muele hasta obtener un polvo. Luego se agrega nuevamente agua, para producir una suspensión, y se sopla aire hacia arriba a través de los tanques.
Aquí, se usa la separación química: se agregan productos químicos para hacer que algunos minerales repelan al agua, permitiendo que los minerales floten hacia la superficie, esta espuma se elimina, diseñada para retirar el concentrado de cobre. La segunda etapa de flotación por espuma produce un concentrado de níquel de 10 a 20% de Ni, junto con otros subproductos y ganga.
La fundición reductora es la siguiente etapa, diseñada para recuperar la mayor cantidad de metal posible. La fundición flash es un método común: los concentrados secos se introducen en un horno y se calientan hasta obtener una mata líquida y escoria. A partir de esta etapa, se puede recuperar una mata de sulfuro, que contiene cobalto y níquel (aproximadamente el 70%). El hierro se recupera en la escoria y el azufre en forma de dióxido de azufre. En esta etapa, los procesos de pirometalurgia e hidrometalurgia se pueden usar para refinar los metales. En pirometalurgia, los metales se separan del contenido de la mata mediante el uso de calor, para separarlos de acuerdo a las características químicas y físicas, como el punto de fusión y la densidad.
En hidrometalurgia, los metales se separan en función de la diferencia en solubilidad y las propiedades electroquímicas. Un método común para lixiviar el níquel de la mata, es usar amoníaco a alta presión, produciendo una solución portadora de níquel. Esta solución se calienta para eliminar el cobre, y con el uso de hidrógeno gaseoso a alta presión se precipita el níquel metálico. El níquel remanente en la solución se puede precipitar agregando sulfuro de hidrógeno. Las etapas del proceso de los dos métodos para minerales de sulfuro magmático se pueden encontrar en la Figura 4. También se pueden usar los lixiviados de cloro y ácido para separar y concentrar el níquel, y la etapa final de la hidrometalurgia es la electrodeposición.
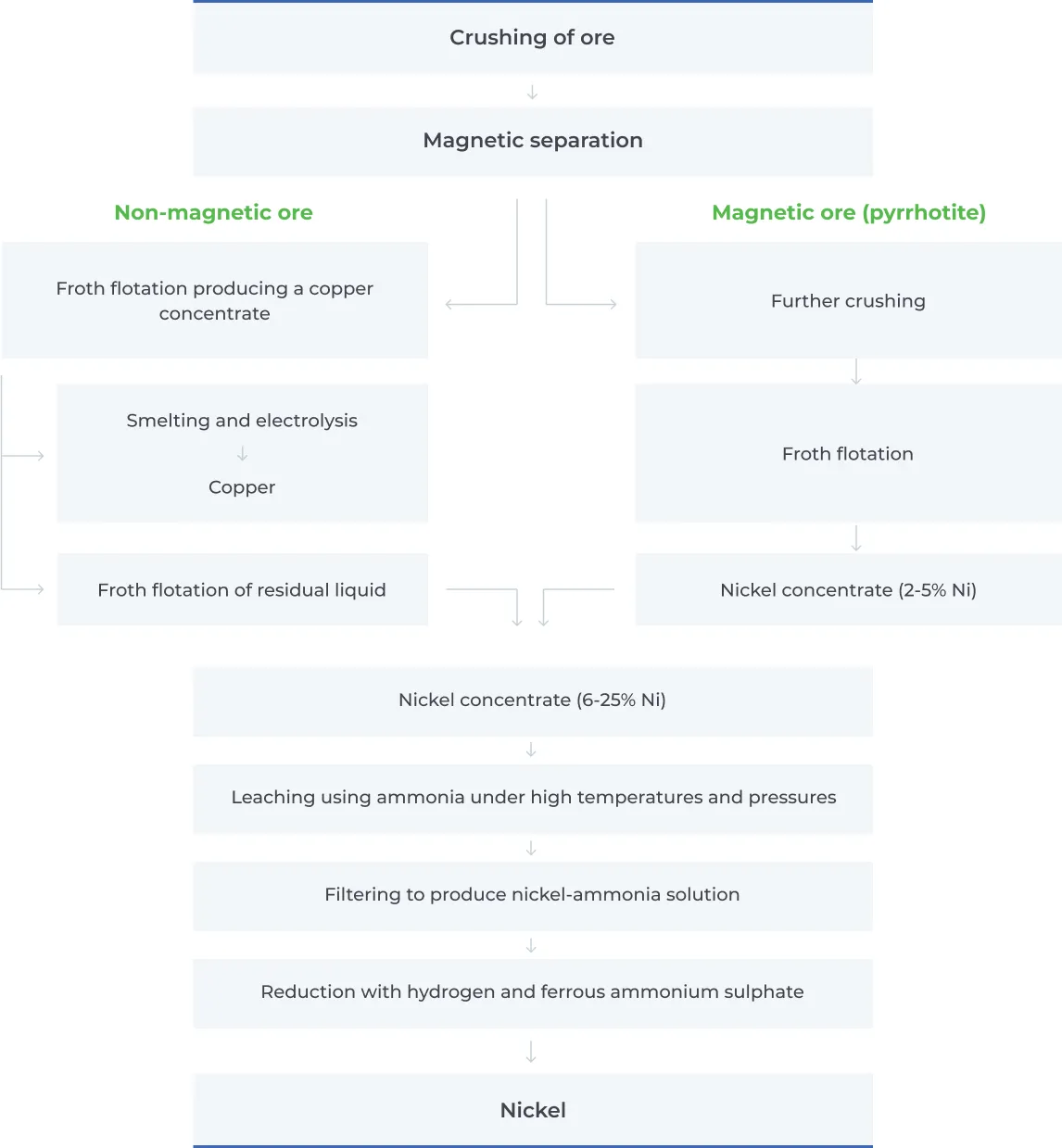
Fig. 4: Hoja de flujo del procesamiento de minerales de sulfuro magnético (Natural Environment Research Council, 2008)
Métodos mejorados de recuperación de níquel
Se están desarrollando nuevos procesos para que sean más rentables y ecológicos. Un ejemplo de esto es Activox®, que elimina la etapa de fundición reductora y emplea una trituración ultra fina y la oxidación a presión del concentrado en un autoclave, antes de la extracción por solvente y la precipitación del metal.
La biolixiviación es otro proceso que se está considerando para minerales de baja ley, ideal para el reproceso en vertederos de desechos. Este método, bajo presión atmosférica, se está usando en el proyecto Talvivaara en Finlandia, un recurso mineral de sulfuro de solo 0.27% de Ni.
Los minerales de baja ley, como el sulfuro de níquel, son abundantes en la Tierra. Los depósitos de sulfuro de níquel contienen altos niveles de minerales de ganga de silicato de magnesio (MgO) y pueden ser difíciles de procesar con las tecnologías de flotación y fundición reductora convencionales. El MgO es hidrófilo, lo cual obstruye la flotación de los minerales de sulfuro y disminuye la recuperación por flotación. En China, el Jinchuan Group Go. Ltd tiene 400 millones de toneladas de minerales de sulfuro de níquel de baja ley, y usa la biolixiviación para la recuperación del níquel. Este método es interesante porque las técnicas tradicionales que usan ácido sulfúrico quedan en desventaja, ya que los minerales de silicato de magnesio son muy reactivos en los medios ácidos, consumiendo grandes cantidades de ácido, lo que aumenta los costos de operación.
Los minerales de níquel de alta calidad están casi agotados, ya que están muy explotados y son menos abundantes que los minerales de baja ley. Los óxidos de níquel de alta calidad se producen mediante el tostado en lecho fluidizado y la reducción de cloruro de hidrógeno de la mata de níquel. Se fabrican pellets de níquel de alta pureza mediante el uso de procesos de vapor, un ejemplo de esto es el proceso de carbonilo: el cobre y los metales preciosos permanecen como un residuo pirofórico, que exige de un tratamiento por separado.
Ya se trate de minerales de níquel de alta o de baja ley, deben procesarse después de la extracción, para mejorar su contenido de níquel de 1 a 4% de Ni a un 10 a 20%. La concentración de los minerales de níquel a menudo se lleva a cabo cerca del sitio de la mina e involucra procesos químicos y físicos para triturar el mineral y separar los minerales que contienen níquel y ganga.
Alta densidad de corriente de la electrodeposición de níquel en Celdas emew
Efectuar la minería directa del níquel es la ruta obvia para obtener níquel puro, sin embargo, el níquel también se puede recuperar como un subproducto de otros metales. Por ejemplo, la electrólisis de cobre necesita de una purga para eliminar el volumen de impurezas que se acumulan con el tiempo como consecuencia de la electrorrefinación del ánodo de cobre impuro para fabricar el cátodo de metal puro. Se necesita una purga cuando ciertas concentraciones de impurezas llegan a ser demasiado altas en el electrolito, afectando de forma adversa el rendimiento de la electrorrefinación. El flujo de purga se retira de forma continua, y se reemplaza con ácido nuevo. La cantidad de purga y la cantidad de ácido de reposición se controlan para mantener el contenido de ácido sulfúrico por debajo del 10%. Este flujo de purga luego se trata posteriormente por neutralización para precipitar los metales que contiene.
El níquel se puede recuperar del flujo de purga de la refinación electrolítica del cobre. Los métodos clásicos para la recuperación de níquel son precipitación, oxidación y cristalización. El níquel y el sulfato tienden a acumularse en el electrolito de la refinación de cobre, y pueden eliminarse por cristalización como cristales de NiSO4 • 6H2O del flujo de purga. Luego se separan del licor madre en una centrífuga, se secan y se les embala para su envío.
En la mayoría de los electrolitos de la refinación de cobre, la concentración de cobre es de 35 a 60 g/L Cu (típicamente entre 40 y 50 g/L), 120 a 200 g/L H2SO4 (típicamente entre 150 y 200 g/L), y 0.3 a 25 g/L Ni. Las impurezas del ánodo soluble se disuelven continuamente en el electrolito, por lo que deben eliminarse continuamente del flujo de purga para evitar que se acumulen. El níquel no es el único metal que se elimina del flujo de purga, también lo son el arsénico, el bismuto, el cobalto, el hierro, el antimonio y de 1 a 2% de cobre (debido a que la corrosión del cobre en el ánodo es más rápida que su depósito en el cátodo).
Extracción de níquel de los flujos de purga con SX
Otro método para la extracción de níquel del flujo de purga es el uso de extracción por solvente (SX). Se pueden elegir solventes selectivos de cobre, y se siguen muchos pasos para obtener polvo de níquel y cobre a partir de la purga. El siguiente diagrama de se mostró en un documento de A. Agrawal et al., en 2012, demostrando los pasos de la SX para la recuperación de níquel y cobre, Figura 5.
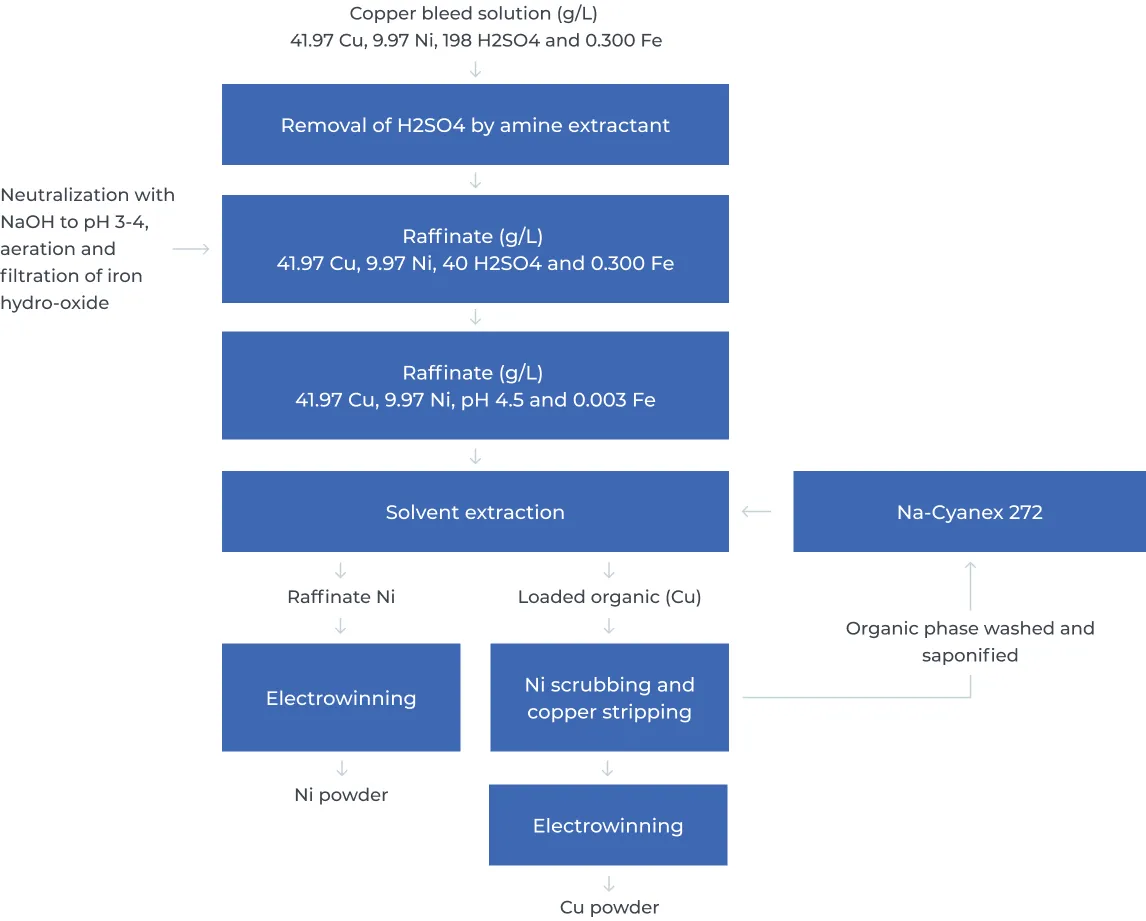
Fig. 5: Diagrama de flujo para el tratamiento del flujo de purga de cobre mediante la extracción por solvente (A. Agrawal et al., 2012).
SX es una herramienta utilizada en el procesamiento de recursos de metales no ferrosos complejos y secundarios debido a la facilidad de separación, purificación, enriquecimiento y análisis de metales. De manera similar al proceso que se muestra previamente, se pueden usar ciertos solventes para extraer primero el cobre, luego ajustar el pH de 9 a 10 para la extracción de níquel. Las plantas SX de cobre son comunes, y son una operación de circuito cerrado, de modo que usan la lixiviación y la electrólisis para producir metal, mientras reciclan los reactivos en el sistema. Por ejemplo, la SX puede usarse para extraer y separar níquel y cobalto de soluciones de cloruro, amonio y sulfato. Queensland Nickel usa una ruta SX en la que el cobalto se elimina como un sulfuro mediante un reactivo, luego el níquel cargado se elimina con una alta concentración de solución de amoníaco y carbonato de amonio, y la solución depurada se usa para obtener carbonato de níquel básico.
Las soluciones de amonio se usan en la extracción hidrometalúrgica de metales básicos porque el hierro y el manganeso se rechazan en el residuo, las soluciones sin estas impurezas pueden someterse a la separación de metales por SX. Algunos ejemplos de soluciones de amonio incluyen nódulos oceánicos, lateritas de níquel, concentrados de sulfuro, chatarra de superaleación y otros materiales de desecho, y soluciones de sulfato.
El ácido sulfúrico es el medio más común para la extracción hidrometalúrgica de metales. Se sabe que a menudo, los procesos de SX separan al níquel y al cobalto de la solución diluida de ácido sulfúrico. Esta separación se lleva a cabo mediante reactivos del tipo de intercambio catiónico. El intercambio iónico (IX) se usa con frecuencia en las industrias de acabado de metales para la recuperación de níquel. Algunos estanques de alimentación para la refinación del cobre también usan el IX para la recuperación de ácido, lo cual implica el tratamiento del flujo de purga refinación, desde las celdas liberadoras con sistemas IX de lecho corto, para obtener una porción de ácido concentrado que se recicla en el estanque de alimentación y un flujo de subproducto libre de ácido. Este flujo libre de ácido contiene metales impuros, así como valiosas sales de níquel que pueden tratarse posteriormente para la recuperación de níquel, con el uso de la electrodeposición para obtener níquel metálico o de la evaporación/ cristalización para obtener cristales de sulfato de níquel.
Producción de polvo níquel y cobre mediante la reducción con hidrógeno
Otro método de obtención de polvo de cobre y níquel, registrado en 2008 por A. Agrawal et al., usa reducción con hidrógeno. Este método toma la purga de cobre y usa hidrógeno gaseoso para obtener cobre en polvo. El licor madre con solución de sulfato de níquel se somete a precipitación de cobre con sulfuro de sodio para eliminar el cobre restante, seguido de la evaporación y cristalización para obtener cristales de sulfato de níquel. El níquel se vuelve a lixiviar con amoníaco seguido de una reducción con hidrógeno para obtener níquel en polvo, Figura 6. La reducción de los iones metálicos acuosos con hidrógeno a altas temperaturas y presiones, puede generar partículas esféricas, y la reducción con hidrógeno del níquel se puede efectuar a partir de diferentes soluciones acuosas.
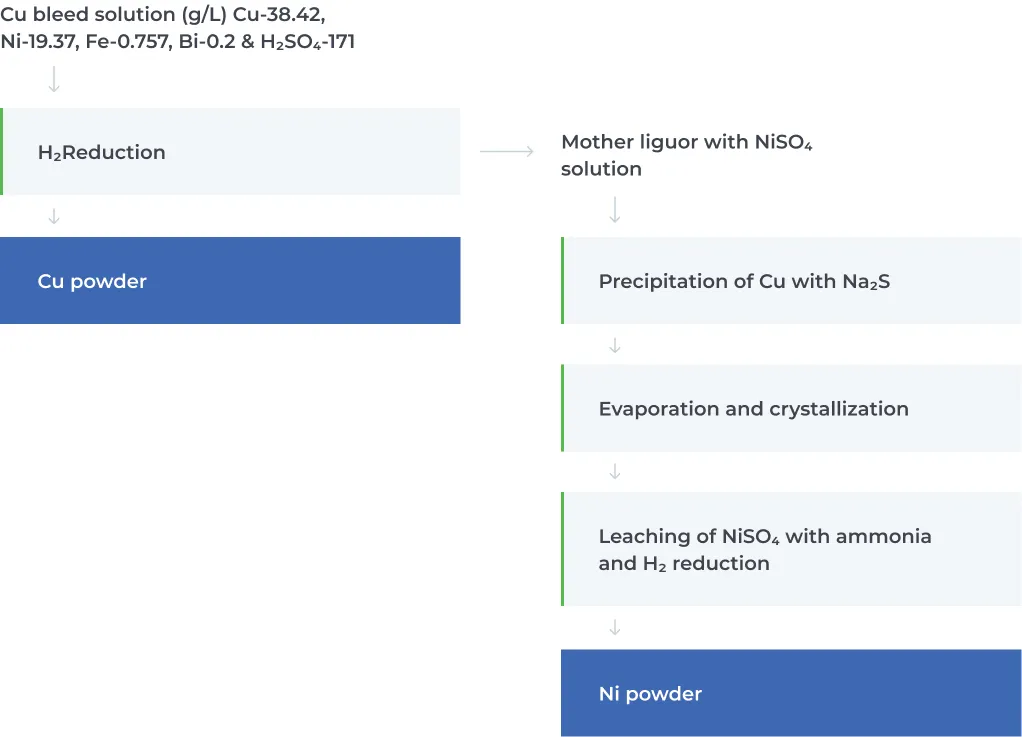
Fig. 6: Diagrama de flujo para el tratamiento del flujo de purga de cobre mediante la reducción con hidrógeno (A. Agrawal et al., 2008.)
En general, apenas he expuesto generalidades en relación a los métodos de recuperación del níquel. Debido a que los minerales de níquel de alta ley son muy escasos en la actualidad, el tostado en lecho fluidizado y la reducción con cloro-hidrógeno en la mata de níquel se están convirtiendo en técnicas menos populares. La recuperación de níquel de minerales de baja ley es cada vez más importante, a partir de las nuevas técnicas de oxidación a presión del concentrado en autoclave, hasta la biolixiviación del níquel en el mineral, es evidente que se están invirtiendo tiempo y dinero en investigar estos procesos. La extracción con solvente y el intercambio iónico también se usan en la recuperación de níquel de varios flujos de purga procedentes de la electrorrefinación de otros metales, como el cobre. Las propiedades únicas del níquel, como la resistencia a la corrosión, las propiedades conductoras y magnéticas, y la capacidad de blindaje electromagnético, hacen que el níquel sea un recurso tan valioso. A futuro, cobrará mayor importancia la recuperación y reciclaje del níquel de fuentes secundarias, conforme disminuya la ley del mineral y se agoten los yacimientos principales.
Referencias
Agrawal, A., Bagchi, D., Kumari, S., Kumar, V. and Pandey, B. (2008). Hydrogen reduction of bleed stream of an Indian copper industry to produce nickel powder. Materials Letters, 62(17-18), pp.2880-2882.
Agrawal, A., Kumari, S., Parveen, M. and Sahu, K. (2012). Exploitation of Copper Bleed Stream for the Extraction and Recovery of Copper and Nickel by Bis(2,4,4-trimethylpentyl)phosphinic Acid. Mineral Processing and Extractive Metallurgy Review, 33(5), pp.339-351.
Agrawal, A., Manoj, M., Kumari, S., Bagchi, D., Kumar, V. and Pandey, B. (2008). Extractive separation of copper and nickel from copper bleed stream by solvent extraction route. Minerals Engineering, 21(15), pp.1126-1130.
Anon, (2010). Mineral Commodity Summaries: Nickel. [online] Available at: https://minerals.usgs.gov/minerals/pubs/commodity/nickel/mcs-2010-nicke.pdf [Accessed 31 July 2017].
Anon, (2012). Mineral Commodity Summaries: Nickel. [online] Available at: https://minerals.usgs.gov/minerals/pubs/commodity/nickel/mcs-2012-nicke.pdf[ Accessed 31 July 2017].
Ambatovy.com. (2014). Ambatovy | Overview. [online] Available at: http://www.ambatovy.com/docs/?p=373 [Accessed 31 Aug. 2017].
Ashcroft, G. (2017). Nickel Laterites: The World’s Largest Source of Nickel. [online] Geology for Investors | Make sense of mining company investments. Available at: https://www.geologyforinvestors.com/nickel-laterites/ [Accessed 31 Aug. 2017]
Cheremisinoff, N. (2007). Handbook of solid waste management and waste minimization technologies. Norwich, NY: Knovel.
Cornwall, H. (1966). Nickel Deposits of North America. [ebook] Washington: United States Government Printing Office. Available at: https://pubs.usgs.gov/bul/1223/report.pdf [Accessed 31 July 2017].
Crundwell, F, Moats, M, Ramachandran, V, Robinson, T, & Davenport, WG 2011, Extractive Metallurgy of Nickel, Cobalt and Platinum Group Metals, Elsevier Science, Oxford. Available from: ProQuest Ebook Central. [31 July 2017].
Dalvi, A., Bacon, W. and Osborne, R. (2004). The Past and the Future of Nickel Laterites. PDA 2004 International Convention. Trade Show & Investors Exchange.
Encyclopedia Britannica. (2017). laterite | geology. [online] Available at: https://www.britannica.com/science/laterite [Accessed 31 July 2017].
Ikotun, B., Adams, F. and Ikotun, A. (2016). Application of three xanthates collectors on the recovery of nickel and pentlandite in a low-grade nickel sulfide ore using optimum flotation parameters. Particulate Science and Technology, 35(4), pp.462-471.
Jones, J. (2017). Nickel Powders from the Carbonyl Process. [online] AZoM.com. Available at: https://www.azom.com/article.aspx?ArticleID=499 [Accessed 31 July 2017].
Kumar, V., Sahu, S. and Pandey, B. (2010). Prospects for solvent extraction processes in the Indian context for the recovery of base metals. A review.Hydrometallurgy, 103(1-4), pp.45-53.
Natural Environment Research Council (2008). Nickel Mineral Profile. Keyworth, Nottingham, UK: British Geological Survey, pp.1-9. Available at: http://www.bgs.ac.uk/mineralsUK/statistics/mineralProfiles.html
Nickel Institute. (n.d.). Where & Why Nickel is Used. [online] Available at: https://www.nickelinstitute.org/NickelUseInSociety/AboutNickel/WhereWhyNickelIsUsed.aspx [Accessed 31 Aug. 2017].
Schlesinger, M. and Biswas, A. (2011). Extractive metallurgy of copper. Kidlington, Oxford, U.K.: Elsevier.
Sen, P. (2015). T.T. Chen Honorary Symposium on Hydrometallurgy, Electrometallurgy, and Material Characterization, edited by Shije Wang, John E. Dutrizac, Michael L. Free, James Y. Hwang, and Daniel Kim. Materials and Manufacturing Processes, 30(8), pp.1051-1052.
Wang, E. (2016). China imports of Philippine laterite ore hit in year of DENR audit. [online] FastMarkets. Available at: https://www.fastmarkets.com/base-metals-news/asia/2016-review-china-imports-philippine-laterite-ore-hit-year-denr-audit-125904/ [Accessed 31 July 2017].